Moisture Balancing Act.
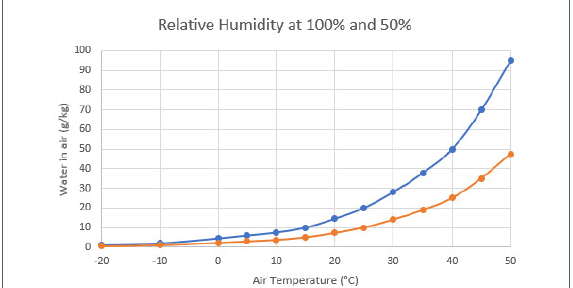
A growing population, high property values, housing shortages, and increased occupation density have contributed to marked changes in the way we occupy homes in the UK. Alongside these changes other factors have impacted on the internal environment of homes. For example, the cost of fuel has risen rapidly which has helped to drive measures for greater fuel efficiency supporting international obligations on carbon reduction. These Government backed programmes that deliver insulation and draught proofing have also changed the ability for some buildings to shed atmospheric moisture. As a result, moisture related issues such as condensation and mould are becoming more commonplace in UK dwellings and disputes between landlords and tenants over causes of dampness are happening more frequently.
Moisture held in the air has always been of great importance to all surveyors. Whilst the ventilation industry and building regs has moved a very long way to satisfy the needs of housebuilders, people in older houses and flats still struggle with moisture-related problems such as condensation and mould.
In the past, condensation and mould growth problems have rather flippantly been dismissed as a problem created by the occupant. However, these problems can be complex with alteration to moisture production impractical. In many instances, adjustments to heating and ventilation are easier than moisture production alterations if there is no obvious excessive source of moisture.
Understanding how to balance moisture production, insulation, energy input (heat) and ventilation as well as a good technical understanding of the science of air moisture and condensation is the key to eliminating condensation and mould.
Condensation and mould growth problems are often multifaceted and a whole house approach should be adopted to establish the root cause of the problem. This should include the entire building envelope and not just the internal atmospheric conditions.
For example, during the external inspection it is vital to identify variations in construction which may result in areas of different thermal properties. For example, outriggers on Victorian terrace properties are frequently constructed of 4.5 inch (112mm) single skin brick work and are a classic example of variations in construction which may contribute to mould growth.
External observations may help assist in identifying possible cold bridges, for example, concrete lintels above windows and doors. Notes of these areas should be made on the site notes and checked internally for temperature differentials.
Insulation
The drive to reduce energy use and increase thermal performance in dwellings has, in part, been achieved by the control of draughts and the controlled release of moisture through the fabric of the building. In some situations, this has resulted in properties that are incapable of managing atmospheric moisture during periods of high moisture production. It therefore follows that the planned management of atmospheric moisture through forced or passive ventilation must be designed around the use and occupation style of the dwelling.
Any retrofit insulation measures should be noted during the external checks. Whilst the insulation helps to regulate internal temperature, the surveyor should be ensuring that the insulation is continuous and that no cold bridges have been formed as a result of discontinuity in the insulation. These are typically found around windows or at the base of walls where the insulation has been terminated above the level of the damp proof course.
Relative Humidity
Relative humidity is one of the key factors in mould growth and provides a good indicator of the environmental conditions.
Air normally contains water vapour in varying quantities and its capacity to do so is related to temperature. The warmer the air the greater its capacity to hold moisture. The amount of moisture in the air is usually expressed as Relative Humidity (RH), which is a percentage of the maximum amount of water vapour the air has the capacity to hold at a given temperature.
Air is saturated when it cannot contain any more water vapour at the existing temperature; under these conditions it is said to have reached a relative humidity of 100%.
If the temperature of the air falls until saturation point, the air is at a critical temperature at which it cannot hold any more water. This temperature is known as the dew point. At this temperature it will result in water vapour being forced to condense out as liquid water. Figure 1 shows the variation in the amount of water air can hold across a range of temperatures. We can see that at 20°C a kilogram of air can hold a maximum of around 15g of water. Relative humidity of 50% at this temperature means the air is holding around 7.5g of water. The graph also shows that as the temperature drops the dew point of the air also drops. This explains why warm, moist air ‘hitting’ a cold wall/window will cause condensation.
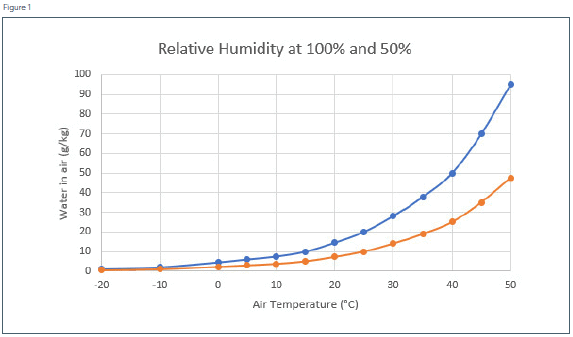
As RH is governed by temperature, care should be taken when using RH in isolation as variations may be a result of varying temperature and not an increase in moisture.
Mould
The main requirement for the development of mould is a source of moisture. However, food, oxygen and temperature are also important. The susceptibility of a material to allow mould growth will vary.
Approved Document F gives an indication that if the relative humidity is sufficiently high for prolonged periods, then mould growth can occur. The table below is taken from Approved Document F and indicates the relative humidity criteria required for mould growth to occur. This table also highlights the significance of time in the potential for mould growth.
Indoor air relative humidity | |
Moving average period | Room air relative humidity |
1 month | 65% |
1 week | 75% |
1 day | 85% |
One important factor is that these figures are considerably less than the 100% RH that is required for surface condensation to occur. The presence of liquid water is not required for mould growth. With a suitable substrate and adequately high relative humidity levels, mould spores will germinate and growth will occur.
Using RH whilst surveying
Armed with the information above it is possible to determine if condensation is occurring at the time of a survey. However, as previously indicated due to the time constraints and the fluctuating nature of RH, long term monitoring provides a better indication if the conditions are consistent enough for mould growth.
With the aid of a surface thermometer and hygrometer to measure wall temperature and relative humidity within a room, it is a comparatively simple matter to establish whether the surface temperature is at or below the dew point, and this will help determine where condensation is possible. Due to restricted airflow in corners and behind furniture, these areas are typically cooler and would be a logical first place to take surface temperature readings. Taking readings from the centre of the wall will not necessarily be representative of these areas. It therefore goes without saying that a hygrometer and surface thermometer are essential pieces of diagnostic equipment for any surveyor who evaluates defects in the built environment.
Vapour pressure and moisture production
Vapour pressure or equilibrium vapour pressure is the pressure at which water vapour above water is in thermodynamic equilibrium with its liquid state. At a higher pressure the water vapour would condense. See Figure 2.
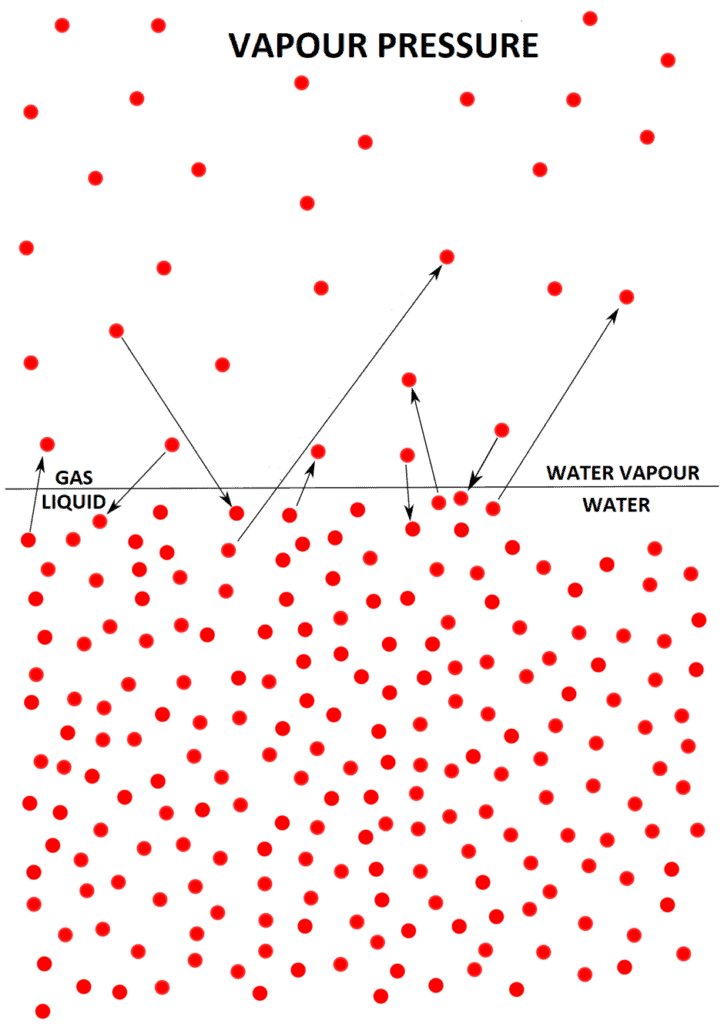
Figure 2
Unlike relative humidity, vapour pressure represents a quantifiable amount of moisture, not a proportion, and can be used to determine levels of moisture production in relation to ventilation. This can be determined by establishing the internal relative humidity and temperature and using a conversion factor to determine the vapour pressure. This exercise is repeated with external relative humidity and temperature.
Subtracting the external vapour pressure from the internal will provide a vapour pressure differential. Due to moisture production created by human activity in winter months within the built environment e.g. showering, cooking etc, moisture levels within the indoor environment are normally higher than external.
Average vapour pressure differentials of 0.45kPa (kilopascal) might be acceptable, although other data may be required to build up a more detailed picture. Below 0.45kPa would typically be considered “dry” or acceptable where ventilation balances moisture production. Above 0.6 kPa would be considered “wet occupancy.”
It is critical to remember that RH and vapour pressure data obtained during the course of a snapshot survey will also be limited in its nature. Furthermore, it is rare that the surveyor is on site at the optimum time when the conditions for condensation and mould growth are occurring. In addition, the use of purge ventilation such as opening windows is commonly used when an inspection is anticipated which results in data which is not reflective of the occupant’s day to day living.
Data logging over extended periods of time can provide better quality information and help to build a more accurate picture of the typical moisture production within the property.
Ventilation
Ventilation plays a vital role in the control of humidity. Failure to adequately ventilate a property properly can result in indoor air quality issues including condensation and mould growth. On the other hand, too much ventilation may result in heat loss and reduced energy efficiency.
The amount of fresh air required will be dependent on the dwelling and the number and lifestyle of occupants within it. An appropriate supply of fresh air is also important to control pollutants and to ensure the safe and efficient operation of some combustion appliances i.e. gas fires etc.
Building Regs
Approved Document F – Means of Ventilation is perhaps the least enforced of all the building regs, which seems a little strange when we consider the significant impact it can potentially have on the health of the occupant.
The requirements in Building Regulations Approved Document F have made strides in reducing the problems in the modern housing stock. However, houses that predate the current 2010 version of this document (that’s the vast majority of the UK housing stock) may have inadequate ventilation.
In theory, properties built after 2010 should comply with the Building Regulations and be provided with adequate means of ventilation. The reality is that there is very little enforcement of the regulations, and problems in properties since this date may arise.
A logical place to start in post-2010 properties with mould would be to see if the system has been installed and commissioned in accordance with Approved Document F. A record of this should have been provided to the occupants.
Judging the right amount of ventilation can be difficult – essentially the only guidelines which are available are in Approved Document F. Ideally a surveyor should always be equipped with a hygrometer to determine the efficiency of a ventilation system.
Ducting
A number of recent studies have found that ducting is one of the single biggest causes of ventilation failing to meet the minimum standards with flexible ducting being one of the worst offenders.
Heating
The heating system can play a significant role in dampness problems and should be able to maintain constant air and surface temperatures. This will assist in the prevention of problems associated with excessive moisture. A modest but constant background heat is preferable to intermittent heating since this will help to maintain a higher ambient temperature in the fabric of the building. The surveyor should take note of the type of system and location of heating elements. During a “snapshot” survey it may be difficult to determine problematic heating regimes, whilst long term monitoring will provide a better picture of the heating regime.
Different heating methods pose different problems, but the inconsistent use and nature of some heating methods can be one of the biggest causes of problems with condensation and mould growth.
Heating the air alone is unlikely to be a satisfactory solution, not only on grounds of cost but also of practicality. Unless cold surfaces are eliminated, condensation at some point is inevitable. Any remedial action, therefore, must involve lowering the moisture levels and the elimination of cold surfaces.
Never one dimensional
Condensation and mould growth problems should never be considered one dimensional. A surveyor must consider the entire building envelope as well as a number of internal parameters. The heating regime plays an equally important role to the ventilation and likewise with moisture production.
This article has focused solely on investigation rather than remediation and for good reason. These problems can be complex, and we should be moving away from the idea that a “one shot kill” is the best way forward and place greater value in long term monitoring. This approach is frequently desirable as the better the quality of diagnostics, the more effective the remediation strategy that can be adopted.