Removing Cavity Wall Insulation.
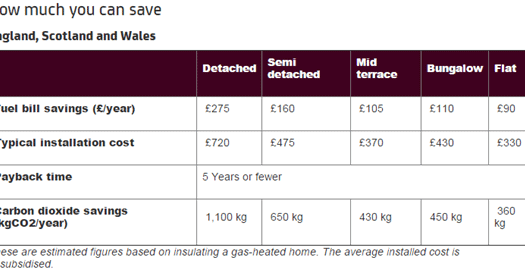
Looking at how cavity wall insulation can be removed
In Issue 20 of the SAVA Technical Bulletin (published in November 2015) we published an article on cavity wall insulation (CWI) and specifically asked the question does cavity wall insulation cause damp.
In this article Chris McGinn discusses if Cavity Wall insulation should be removed and how this would be done.
Is CWI fit for purpose?
We addressed this question in detail but to recap here the simple answer is yes, if properly installed and if the materials have been tested and certified. The Energy Savings Trust has calculated how much an occupier could save if the insulation is correctly installed.
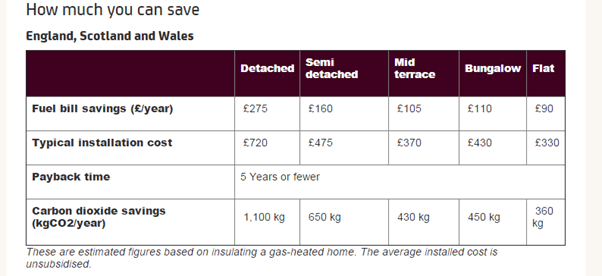
(Source: Energy Saving Trust – www.energysavingtrust.org.uk )
The issue for surveyors is to recognise that CWI has been retrofitted and to be alert to situations where CWI may have been inappropriately or incorrectly installed and understand the options available to the home owner if this is the case.
Why the CWI?
Various government backed schemes energy efficiency schemes such as The Energy Company Obligation (ECO), the Carbon Emissions Reduction Tart (CERT) and the Community Enery Saving Programme (CESP), have resulted in significant take up of cavity wall insulation, with home owners being offered significant discounts on installations as a drive to using less energy.
Although the government subsidised schemes resulted in firms such as The Mark Group installing insulation on an almost industrial scale, it should be emphasised that vast majority of Cavity Wall Insulation installation companies were not rogue installers or operating under false promises. There are a lot of properties which have had CWI installed without any issues at all and customers report that the house is warmer, and the bills are less.
However, it is a fact that some houses should not have had cavity wall insulation installed or that over the years changes have occurred resulting in cases where the insulation is being reported as having caused damp.
A number of installations should never have been done due to adverse location issues or the fact that the cavity was full of debris, for example. Also, some were not done correctly. At the time of the installation it would be difficult for the customer, or indeed a surveyor appointed by the home owner, to challenge the quality of the work due to the simple fact of not being able to see the finished product as it was inside the cavity.
And it would be simple to blame the companies for installing the materials in inappropriate properties. However, installation companies would only be able to carry out limited pre instal surveys. This is due to the simple fact that they were retrofitting the product into a property that had already been built and while they would have used a borroscope to inspect the cavity prior to installation this would only be done at high risk locations, such as wall junctions, and inevitably not all the cavity would be seen.
We also have to acknowledge the commercial pressures on the installation companies which would have been subject to meeting volume targets on relatively low margins.
There are varying estimates of how many properties have either been incorrectly installed, or should never have been touched. Estimates range from the bottom end of tens of thousands, up to the millions depending on who is reporting. So surveyors have little to guide them and must rely on their own expertise and the results of careful inspection.
Should CWI be removed?
Once the insulation in a property has got wet, this will impact on the efficacy of the insulation. Just 1% moisture content within insulation will make the house actually feel colder than it did before the insulation was installed.
Moisture gets into the cavity via a number of routes, but when it is in a cavity which has had CWI there is not enough air circulation to allow the water to evaporate as it would have done previously.
Indications that suggest that the insulation might need to be removed include:
- · High exposure areas
- · Cold spots and voids where a temperature imbalance has occurred
- · Rubble and blockages within the cavity
- · Bridging of the cavity / penetrating damp
- · Flood damage
- · Compromised DPC
Whether the cavity can be refilled is then open to the same conjecture that was present before the original installation took place. It is to be noted, that with a different product, and any original issues resolved, it may be suitable to insulate the cavity once it has dried out.
Who should remove the insulation?
Many ex insulation installers are re-branding themselves as extraction specialists. However, unlike CIGA which regulates the product insulation in the first place, up to now there has been no regulation of extraction companies.
Until recently there has been no industry standard for cavity extraction or a framework to monitor the companies doing the extraction work. However there is now there is a cavity extraction competent persons’ scheme (CPS) operated by Stroma.
Stroma runs a number of competent person schemes. The accreditation for Cavity Insulation extraction involves a combination of the below, which are pooled to gauge whether a company is competent to carry out the work they claim to.
- · Review of company processes and documentation (Method Statements, Risk Assessments etc)
- · On Site Competency Assessment Report – known as an OSCAR, which is an assessment that the operatives are capable and competent to carry out their work to a high and safe standard
- · System Design Carding – to ensure the operatives are trained and carded by the designer of the machinery they use on site.
In addition all extractions are lodged with Stroma who carry out random audit checks.
How is the Insulation Removed?
Previously, Insulation removal has proved somewhat of a cumbersome and labour heavy task, often involving cutting out diamonds of bricks and removal of the insulation by hand. Sometimes cavity install machines have been used, with a suck mechanism rather than blow.
The method favoured by accredited extraction companies is to use a machine designed specifically for removing insulation from cavities. In simplistic terms, the method of extraction involves sealing all gaps within the wall space to pressurise the cavity, including open cavities in the loft space, and small air gaps inside the properties, eg. under window sills. Small drill holes are then inserted into the wall (similar to the drill pattern of the install) A compressor pumps high air pressure through a hose, which has a specifically designed “whip” attachment at the end. This whip then works in a propeller motion within the cavity to agitate and loosen up the insulation. Once the insulation has been loosened up, the whip is replaced with a directional nozzle, which uses the same high air pressure to direct the insulation to the collection point. The collection point will generally be at the bottom of the wall, where a single brick is removed, and the CLC200 sucks out the loose insulation. The collection hose has a specifically designed brick connector, which fits perfectly into the gap created by the removed brick, thus reducing the risk of losing air pressure in the cavity.
This method works well with most insulation material, including particle fill (beads), fibres (mineral wools, white wool), and open cell foams. However, some foams used in the past are renowned for setting to an almost rock hard formation (closed cell foams) , and almost become part of the structure of the wall. In these cases, other options for extraction will need to be explored. Tests should always be carried out to see whether a material can be removed prior to extraction – typically during the pre-extraction survey.
About the Author
Chris McGinn is a qualified Domestic Energy and MD of All-Building Energy Solutions. He has been in the energy industry for the last ten years and more recently has worked on renewable and boiler schemes. Having seen first hand the damage to some properties caused by inappropriate insulation, Chris believes that extraction should be carried out by firms competent to do so.
He is studying for the Diploma in Residential Surveying and Valuation through the SAVA School of Surveying and Bluebox Partners with a view to becoming an Associate Member of RICS.