Chimneys and Flues – Defects and How to Report.
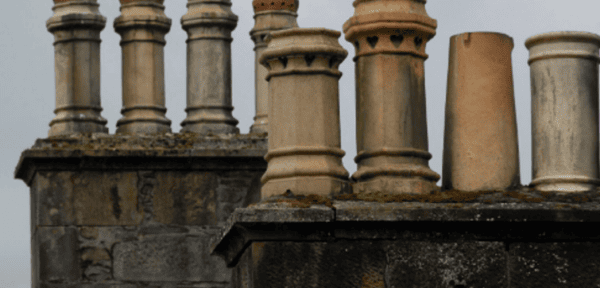
Hilary Grayson looks at the evolution and construction of chimneys and flues and the type of defects which can arise. It covers obstacles presented to the surveyor with additional comments from Chartered Building Surveyor, John Wheatley, regarding hygroscopic salts and damp on chimney breasts.
Virtually all houses built before the 1960s would have had a chimney. With an increase in gas fires and central heating and the labour involved with lighting and cleaning open fires, the open fireplace and chimney became redundant. As a result, many properties were ‘modernised’ after the 1960s by removing or bricking up fireplaces and removing the hearths and fire surrounds. Houses and flats built after this time were usually built without fireplaces and flues at all. However, there has been a revival of the traditional fireplace and surround, both for ornament and as a supplementary form of heating. If a homeowner has ambitions to ‘open up’ a previously bricked up fireplace, reinstate an open fire or install a wood burning stove and they run into problems, they could take their frustrations out on the surveyor who carried out the pre-purchase survey. In this article, we look at flues and chimney breasts and at some of the things that can go wrong.
Evolution of the chimney
Early homes relied on a wood burning open fire as the sole heating source. This would usually consist of a plain stone hearth and vent through a hole in the roof or wall. Where the vent was through a roof this was sometimes covered by a louvre to stop the rain getting in. Chimneys were not widely adopted until the Tudor period, and even then, only by the upper classes (a good example of the early chimney stacks are those at Hampton Court Palace) while more domestic buildings still dealt with smoke-filled rooms.
During the 16th century timber supplies were not so available, and coal became a more commonly used fuel. As coal smoke is toxic, more sophisticated ventilation was required, and the chimney became more commonplace.
Early chimneys were not particularly efficient and were often very dangerous, as their construction from wattle and daub was susceptible to fire. Following the Great Fire of London in 1666, further changes to chimney construction were made. By the early 1700s all clay-built chimneys in England were ordered to be rebuilt in brick.
However, a poor understanding of combustion toxic gases meant that chimneys were still inefficient and significantly contributed to air pollution over the increasingly industrial cities. By reducing the size of the fireplace, introducing angled sides to reflect heat back into the room, and restricting the flue size to increase airflow, efficient fireplaces and grates were developed.
This new, improved fireplace could be built inside the large and inefficient fireplace openings that already existed. For new installations it could be incorporated into the wall. It’s only recently that small, comparatively efficient, coal-burning grates and fireplaces were developed. This is the type of fireplace commonly seen in Georgian, Victorian, Edwardian and early 20th century houses. Some were quite ornate, with beautiful tile panel inserts, which were replaced by tiled fire surrounds in the 1920s and 1930s. These continued to be popular until the demise of open fires in the 1960s.
Construction of the chimney and flue
The chimneys most surveyors will find are in houses dating from the late Georgian period up to the 1950s. The fireplaces, chimney breasts and flues will usually be of brick construction. Even in a stone wall the chimney itself is likely to be of brick because of its durability and flexibility. Most chimneys were built at the same time as the walls and the brick flues were usually the standard length of a brick internally (225mm/9”).
Chimney flues can be complex. For example, a ‘mirrored pair’ of houses share one chimney stack, but each house could have four open fire places. This would mean eight flues ultimately emerging at the chimney stack. It was quite an art for the bricklayer to connect the right flues to the right fireplaces and make sure that they all avoided each other. For this reason, flues in older properties rarely run in a completely vertical line from bottom to top. Usually the flues will be off-set at some point to avoid the fireplaces on the floors above.
The thin walls between the flues in a single chimney are called ‘withes’. Where a flue has to ‘bend’ to follow the direction of the chimney or allow for another fireplace in the room above, the bricks in the ‘withes’ will be stepped or ‘raked’.
If the brick work was of good quality then the outer chimney wall will be one brick thick, but half brick thick is by far the most common, since the vast majority of terraced Victorian housing we are used to seeing in British towns was ‘housing for the masses’.
In houses built since the introduction of the 1965 Building Regulations, all flues must be built with liners during their construction. These will usually be clay liners, which should last the life of the building.
Prior to 1965 construction was controlled by locally accepted good practice or local byelaws. This means that there can be local variations. Prior to 1965 flues were usually rendered on the inside. This was called ‘parging’ and would have been with a lime mortar.
Downsides of burning coal
Burning coal causes many problems due to the gases released during combustion. Traditional lime render used in flues was not air tight and affected by the acids and tars produced during combustion, causing it to gradually deteriorate. This leaves the flue in poor condition, often leaking fumes or tars into the walls or other parts of the building. Despite the building regulations, houses built after 1965 can suffer similar problems due to badly installed flue liners. Cracked flue linings can eventually fail, causing render to fall down the chimney leading to rubble in the fireplace.
The acids and tars produced by burning coal can also affect the bedding mortar between the withes. This causes bricks to loosen and sometimes crack. If bricks within the withes are displaced, flues are no longer properly separated and can develop smoking and downdraft problems. Chimney sweeping can also cause damage to bricks, particularly if they have been loosened due to burning coal.
Hearth construction
If a chimney will be used as an open fire or a stove, then the hearth should be made of suitably robust materials. It should also be at an appropriate size to protect the rest of the building. Sometimes fireplaces were removed, and hearths left in situ. You’ll also find some were altered to make the floor area flush with the newly bricked up chimney opening.
See Document J in the Building Regulations for more information on how to reconstruct an old hearth for reuse.
Challenges for the surveyor
More recently, there has been a resurgence in open fires. Many new houses are now built with at least one working fireplace. For example, a wood burning stove is often described by estate agents as a ‘feature’ of a property.
Therefore, surveyors must understand how flues and fireplaces work and be aware of the issues that a homeowner might have to address if they wish to re-instate an open fireplace or install a stove. Many surveyors report that they are often asked by the purchaser to look at the practicalities of opening sealed fireplaces and re-using redundant flues when conducting building surveys or condition reports. This is supported by the use of the Sava Fact Sheet on wood-burning stoves. It is one of the more popular and many surveyors use it to provide their clients with more generic information. You can download the factsheet from Sava EDGE here.
Assessing the inside
When a surveyor inspects a building, they won’t be able to accurately assess the inside of the flue. If a fireplace is open and accessible it’s sometimes possible to look up the flue, but often it’s blocked off to prevent drafts and keep the room warm. A ‘clean’ fireplace does not necessarily mean that the flue is relatively intact.
Ventilation and rainwater
Removing the original fireplace can also lead to other problems. The old-fashioned open fireplaces provided efficient ventilation, which is essential to remove toxic coal gases. Even when the fire was not in use the flue would promote air movement and ventilation – warm air rises and so would rise up the flue and escape through the chimney. While not desirable in terms of energy saving, this would have reduced condensation.
Other problems caused by flues include rain getting into the open top. If a fire is lit regularly, then this is not a problem as the heat will keep the chimney dry. However, if fireplaces are sealed up, there’s nothing to stop rain entering the top of the flue. Without the warmth from a fire, the resulting dampness within the chimney can be a problem. To prevent this, a suitable terminal should be fitted to the top of chimney pots of disused fireplaces, which stops the rain but allows ventilation. If chimney pots have been removed altogether, this could be a sign of careless work when the fireplace was decommissioned and should alert the surveyor to other potential problems in this area.
Ventilation to the flues within the building is also necessary so that air can still enter the bottom of the flue and escape through the terminal on the stack above. When carrying out an inspection it is essential to check that any redundant flues are fitted with suitable terminals at roof level and also make sure that the flues are ventilated inside the house.
It’s also possible that the chimney could have been removed completely below roof level while the stack remains within and above the roof. We all know about Smith v Bush and it is not the intention to consider that case in depth here, suffice to say that if a chimney breast is missing, it is essential that the surveyor follow the trail and try to determine, if possible, that the chimney above the missing element has been supported properly. This is not always possible, particularly if the ground floor chimney breast has been removed.
Managing Clients expectations
Client expectations can be difficult to manage, particularly when builders and other parties later inform them that: “your surveyor should have spotted this”.
It’s important, where possible, to speak to the customer before the survey takes place. Ask them about the fireplaces and whether they have any specific ambitions. However, this isn’t always possible, and customers may not yet know what they want to do with the property. It can’t be assumed that just because they do not have plans prior to purchase, they will not open an enclosed fireplace later on.
Potential queries
The following are some examples of complaints or queries that could arise post survey: –
• Rubble in a fireplace
• Fireplace is damp
• Unexpected costs of relining a flue or rebuilding a hearth
• Hearth present is not suitable
• Draughts from the chimney
Clearly, surveyors don’t have x-ray vision, but it is possible to inspect, record and report in such a way that pre-empts future problems.
The following precautions can help address queries at a later date: –
• Where chimney pots have been altered or removed, follow the trail to find out why.
• Where flues are redundant, consider if the terminals at the pots are enough to stop water from getting in.
• Photograph and mark on a floor plan any furniture that is obstructing a chimney or fireplace, whether blocked up or not.
• If an electric or gas fire has been installed, make a clear note and take photographs. If it is a gas fire, you also cover it under ‘gas appliances’.
• Use your moisture meter around the base of the chimney breast in all rooms, remembering that all flues would have been built separately. If the fireplace has been blocked up, is it sufficiently ventilated?
• Remember that flues may have bends to accommodate fireplaces above, and dampness can accumulate on those bends – so be alert for signs of damp higher up the chimney breast.
In your report include the following: –
• Highlight any alterations for further investigation – have building regulations been sought and approval given?
• Make it clear what can’t be inspected, and why. This could include flues, closed fireplaces, fireplaces blocked with furniture etc.
• Make it clear that testing the flues is beyond the scope of inspection.
• Make it clear that even if you cannot find anything of concern on the day of the inspection, this does not mean that the flue is in good repair.
• Make it clear that a flue in bad repair can impact on the health of occupants by leaking carbon monoxide into a room.
• For terraced properties, make it clear that the flues will share a chimney with the neighbouring property.
Note on Hygroscopic Salts
Chartered Building Surveyor, John Wheatley says:
“It is very common to find that ‘damp’ on chimney breasts relates to salt contamination of the plasterwork, effectively causing condensation hot spots. The by-products of coal combustion are acids, which react with chemicals in the masonry to form chlorides, nitrates and sulphates. These materials are ‘hygroscopic’, which means that they can absorb water from their surroundings. This usually occurs at or near ordinary room temperature. While most hygroscopic materials are salts, other materials also do the same thing.
“When water vapour is absorbed, its molecules are ‘taken into’ the molecules of the substance, which results in physical changes, such as increased volume. In practical terms, it often means there are patches of moisture left behind as the salts fail to leach out of the brickwork in a consistent pattern.
“I have a good example in our en-suite bathroom. We took down the chimney stack when extending our home but retained the chimney breast as a service duct. The face of the breast was finished with plasterboard on dabs. The plasterer was asked to incorporate salt retardant in the dabs. Around 12 years later, we noticed one small patch of damp every time the shower went on. It disappeared when the humidity dropped back to normal.
“My working assumption is that one of dabs has no retardant and, over time, the salts have leached through. This has caused a condensation hot spot when the humidity levels are high. Six years on, it comes and goes with no real consequence other than a red-faced surveyor and a slightly tutty wife. This would be difficult to spot for a surveyor as it’s not immediately apparent that the service duct is an old chimney breast from the 1920s, and the damp patch isn’t visible most of the time.
“However, it does give a reading on a moisture meter as the salts are conducting, and as we all know a moisture meter isn’t a moisture meter at all – rather it simply records where there is a material that can conduct an electric current.”