Fires Due to Faults in Electrical Cables.
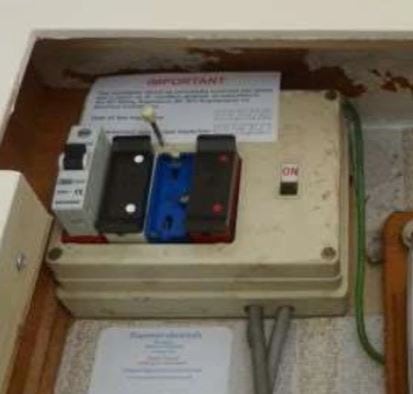
1.0 Introduction
According to a report in the Guardian Newspaper in August this year (and following the Grenfell Fire) it was reported by the London Fire Brigade that nearly one fire a day in London involves faulty white goods. The Fire Safety Council estimates that 89% of electric fires are caused by faulty goods with only 11% caused by faulty installations. Between 2010 and 2016 there have been nine fatalities and 298 injuries as a result of fires involving white goods in London alone. Of course, white goods fall outside the remit of a prepurchase survey but even though the percentage is small other electric faults can expose a property to a risk of fire. This short article looks specifically at how installed cables, and the materials that come into contact with the cables, can increase the risk of fire.
2.0 What are the main causes of failure in electric cables?
There are many reasons why a cable may fail with the risk of igniting a fire. Some of the main causes of cable failure include:
Ageing: The service life of a cable can be significantly reduced if it has been expected to operate beyond the optimal operating conditions it was designed for. Ageing will usually result in the cabling getting brittle and cracking creating failure of the insulating and sheathing materials, exposing the conductor and risking a potential short circuit. This is a potential cause of electrical fire.
Application: If cable selected is not appropriate for the application it is more likely to fail in service. For example, a cable which is not robust enough for the environment, either mechanically tough enough to wear and abrasion or chemically resistant to the ambient conditions, is more likely to fail than one whose construction is suitable for the installation environment.
Mechanical failure or damage: If the cable is damaged either during installation or in subsequent use, the integrity of the cable will be affected and can result in failure described above. Degradation of the cable sheath: There are several reasons why the sheathing material may degrade. These include excessive heat or cold, exposure to chemicals, exposure to inclement weather conditions, and abrasion of the sheath. All these factors can ultimately cause electrical failure as the insulated cores are no longer protected by the sheathing as originally designed.
Moisture in the insulation: If water gets into the cable it can cause significant problems including short circuit and corrosion of the copper conductors.
Heating of cable: Excessive heating of the cable will cause degradation of the insulation and sheathing material and premature failure. The heat may come from an external source or may be generated by the resistance to current flow in the conductor – this is a particular problem if the cable is overloaded and/ or underrated for the application.
Electrical Overloading: Electrical overloading normally occurs when the cable is underrated for the application or when too much load is being placed on the cable. In domestic applications this is often a result of plugging too many appliances into the one socket and overloading the wiring to that individual socket, extension adaptor or gang socket.
Rodent attack: Rodents can nibble at the outer layers of cables. This damage can be extensive, significantly reducing the sheathing or insulation properties of the cable causing another possible source of electrical fires.
UV exposure: UV exposure can have a significant influence on electrical cable insulation and sheathing. Cables likely to be exposed to UV light should either be designed with UV resistant materials with a suitable carbon black content, or protected from exposure with a protective covering ie. cable conduit, not in direct sunlight. UV exposure frequently causes cracking of the insulation and therefore potential short circuit failures.
Fire Case Study from Essex Fire Brigade
The property in question was well looked after and maintained. Early one Sunday evening, the occupier heard her smoke alarm activate. She went to investigate and saw wisps of smoke coming out of the loft hatch on the landing. She immediately phoned the fire service and left the property, shutting the door behind her. When fire crews arrived they discovered a small fire in the loft. This was quickly extinguished with a hose reel. Cause – Electrical wiring It was discovered that electrical wiring had been run across the loft space with sheets of polystyrene insulation laid over the top. Over a period of years the cable insulation became coated in polystyrene as a result of “plasticiser migration”. There was a reaction between the plasticiser in the PVC insulation and the polystyrene, whereby the plasticiser migrated out of the PVC, softening the styrene which adhered to the PVC, leaving a brittle cable that cracked and split. This exposed live conductors which ignited a fire, the fuel being the timbers within the loft space. But for the activation of the smoke detector aiding early intervention by the fire service, the damage to the couple’s home could have been far more severe. Safety message The service life of insulated cables where is contact with polystyrene can be severely reduced. The advice from the fire authorities is that household electrical wiring should be inspected and replaced regularly by a qualified electrician. Care should be taken with any wiring that might be run up the inside of a cavity wall where polystyrene bead insulation has been installed at the property.
3.0 PVC Cables in contact with polystyrene and polyurethane insulating materials
Plasticisers are used in PVC to give the required physical properties such as flexibility and toughness. These compounds are commonly used in TPS (Tough Plastic Sheathed) Power cables, Cat5 & Cat6 data cables and B20 and B95 data cables. Plasticisers are typically non-volatile, high boiling point liquids which are absorbed into the PVC matrix at high temperatures during the manufacture process. However, they are not chemically bonded to the PVC compound and under certain conditions can be extracted from the compound. Commonly used PVC plasticisers can ‘dissolve’ into polystyrene and polyurethane insulating materials. Because they are not chemically bound in the PVC, these plasticisers can move from the PVC compound when there is a direct contact between the two materials. This causes the PVC on the cable to become harder and more brittle, thus making it susceptible to electric fires (see causes of fires earlier in this article).
The Surveyors Responsibility
As already mentioned the greatest risks relating to fire come from white goods, including extension cables etc. Despite the lower risks from the actual installation and the fact that the majority of that installation will be out of sight, surveyors still need to be aware of potential for harm to people or property associated with the installation and specifically the cables.
It would be in scope for the normal inspection in order to produce a Homebuyer report or Home Condition Survey to:
- Identify high moisture in walls adjacent to sockets or other light fittings thereby highlighting additional risks of short-circuiting etc.
- Identify the possibility of rodents with access to exposed cables
- Identify the risk of cables exposed to polystyrene or polyurethane materials (such as spray polyurethane foams in roof spaces etc.)
- Note the excessive use of extension cables by the existing occupiers
Guidance is clear – for ‘services that kill’ where there is no valid and current safety certificate visible at the date of inspection then it is appropriate to apply a Condition Rating 3. While this is ‘best practice’, when auditing Home Condition Surveys in SAVA we see a lot of properties without the relevant safety certificates. Of course we do not know what the homebuyer does with this information, and there is a suspicion that many do not follow it up. Therefore, it could be argued that the surveyor should provide additional information relating to specific risks to people and property, such as those identified here, where they are clearly visible over and above the general CR3 because there is no valid and current safety certificate.
WE LIKE…
The Electrical Safety Council campaigns on behalf of consumers and electrical trade professionals to improve safety regulation and ensure safety messages are appropriate, up to date and well communicated. They are recognised by government and industry as the leading campaigning charity and technical authority on electrical safety. The Electrical Safety Council (Trading name Electrical Safety First) works to ensure that everyone in the UK understands the importance of electrical safety. They campaign on behalf of consumers and the electrical trade profession to improve safety regulation. They cover product recall (not just faulty white goods but also products used in the electrical installation), counterfeit products and product misuse. They take particular note of the more vulnerable in society – the elderly who are disproportionally at risk from electrical hazards in the home, and those in private rented accommodation. They publish a series of downloadable fact sheets and best practice guides. For further information go to https://www.electricalsafetyfirst.org.uk/