Lime Mortar.
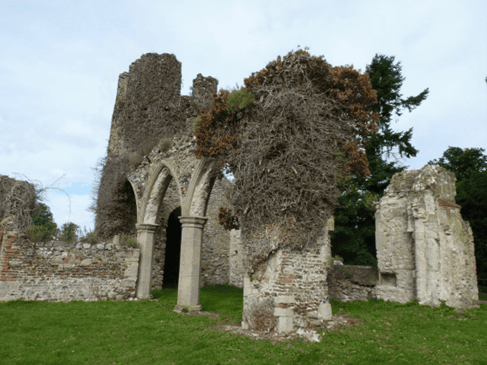
In this article, Bernie Smith MCABE. C Build E. FCIOB reviews the past use of lime mortar and explains the different types available and their benefits. He also shares two interesting case studies where he was appointed a consultant and his company, Smith Building Services, carried out repairs using lime render on historic buildings.
History
Limestone or calcium carbonate (CaCO3) is a naturally produced stone found extensively throughout the world.
The earliest documentation of the use of lime in construction was around 4000BC. It is documented that the Egyptians used lime in the construction of the Pyramids. There is also some evidence of the use of lime when looking at buildings by the Romans and ancient Indians, and confirmation that lime was used when building the WeIzmann Institute in Israel, 12000BC.
All these years ago, it was discovered that if you burnt limestone and then combined it with water, pliable material that hardened with age was produced. There is no definite date affirming when regular use of lime in construction began, but it is documented that the Roman architect Vitruvius provided basic guides for using lime when building. The Romans were keen advocates for using lime mixed with baked clay or volcanic ash, which when water was added, they found would harden considerably, producing a very reliable building component.
Lime continued to be used as a reliable construction material through time, however, in the 18th century, it was discovered that if you fired a limestone that contained clays, this would result in a hydraulic lime. In 1756 a gentleman named James Smeaton developed probably the first commercial hydraulic lime product available on the open market. His method was to combine pozzolans and Blue Lias limestone which contained clay, and he discovered that this produced a strong lime mortar that was very good in harsh environments and had good resistance to severe weather and even salt water. This was what was used to build the Eddystone lighthouse, a structure that has certainly stood the test of time in very harsh conditions.
Benefits of lime mortar
It is the flexibility of lime mortar that makes it so successful for building. Whereas more modern cement-based mortars tend to be much more rigid and unforgiving, lime mortars allow movement within the structure without stress or cracking. Lime mortars also help with the ingress of moisture within a building. Acting with a wick-like ability, this may seem like a disadvantage, but by drawing moisture in it also allows the structure to easily dry out. The fact that the majority of the moisture is taken in and expelled through the joints means there is less chance of spalling of the masonry or a saturated building. The fact that lime mortars allow moisture to enter but also evaporate is very important to buildings that have been constructed without moisture barriers and techniques to allow flexibility, such as damp-proof courses or movement joints. Sometimes when talking about the permeability of a building, you very often hear the expression “the building needs to breathe”. Personally, I prefer the expression “a building needs to dry”; this is simply saying that the structure does not trap moisture within itself, the moisture enters, but it also evaporates. Therefore, there is less likelihood of damp, mould growth or infestation of the fabric of the building.
Lime seemed to go out of fashion during the nineteen sixties, seventies and eighties, with the use of Portland cement being the favourable product used. Although Portland cement has been around since the first half of the eighteenth century, lime mortars and renders were still quite widely used up to this time. During the sixties, seventies and eighties, Portland cement was considered by many to be the right product to use on almost all types of construction projects including, unfortunately, sometimes historic restoration and repair works. Although the process of listing buildings of historical importance came into place during the Second World War, the care and repair of them were not always carried out most sympathetically. Over the last forty or so years, it has been realised that using the right materials for repairing and renovating old buildings is of the utmost importance. It is not just buildings of historic interest but also thousands of other buildings that benefit from the use of lime mortars and renders in their repair and construction.
Lime v cement-based
So, why is it important to use a lime mortar or render, rather than a cement-based product, when working on older buildings?
The first thing to remember is that the material binding or covering the stone or brickwork should not be stronger than the stone or brickwork itself. If the mortar or render is stronger, the building will not be able to flex or move, and damage may occur to its structure.
Secondly, cement-based materials are very dense and not very porous, therefore, any ingress of moisture could become trapped within the fabric and cause damp or structural issues.
Thirdly, when working on old buildings, especially ones of importance, it is important to ensure that the repair or building work does not look out of place and matches the original the best it can. It is easy to spot a repair that has been previously carried out using cement, as it stands out like the proverbial sore thumb.
Different types of lime
Hydraulic lime
When building with lime, the first thing is to decide which lime mortar or render will be most suited to the project that you are carrying out. For historic work, the most popular used is hydraulic lime, in simple terms, hydraulic means operated, moved or affected by water. Hydraulic lime is produced using limestone which hardens when water is added, known as slaked, and once it starts to set, it absorbs carbon dioxide from the atmosphere. The more hydraulic the lime used is, the faster it sets and the stronger it becomes. Hydraulic lime is categorised as follows: NHL2, NHL3.5, and NHL5. The number relates to compressive strength in megapascals (MPa) or newtons per millimetre (N/mm2).
NHL2 is the gentlest and most flexible of the hydraulic limes, it contains less than 12% clay which creates a slower setting time, normally around 20 days in water. NHL2 is normally used for internal works and for making lime plaster.
NHL3.5 is the more general-purpose and moderate lime; it contains between 12% and 18% clay and sets in water around 15 to 20 days. NHL3.5 is suitable for most day-to-day use of lime in construction.
NHL5 is the strongest and most fast setting of the three limes. It contains 25% clay and sets very quickly. If the conditions are right, it can set within hours. NHL5 is suitable for use in more exposed environments. Recently there seems to be a little controversy over the use of NHL5, one school of thought is that over long periods, it is setting too hard and not being as forgiving as predicted. It has been reported that, in some instances, the use of NHL5 has resulted in problems with the build or repair that is taking place. As stated above, this is just one theory and not a common opinion.
Hot lime
Hot lime, sometimes called hot mixed or hot mixed mortar, is another part of the lime construction family. Hot lime is the process of mixing quick lime, aggregate (usually sand) and then slaked. This process creates a powerful exothermic reaction and produces temperatures up to and exceeding 250 degrees Celsius. However, this high temperature only occurs in a low percentage of the mix and the majority of the mix should remain around 100 degrees Celsius. This is obviously where the term ‘hot lime’ is derived. This is the ideal temperature to produce a workable and productive mix.
The advantage of using a hot lime mix mortar over a hydraulic or hydrated lime mortar, is that the hot mix mortar is, to use that word again, more breathable, anything up to twice as much. It will adhere to the subject being constructed a lot more easily. Compared to the other limes, it is usually cheaper to purchase. It is also often specified because of its authenticity and ability to match existing lime-built structures. This is because it is a similar process of producing lime mortar as in historic times, however, modern hot mortar limes are a purer version than previously used.
One disadvantage is that in some situations, the setting times can cause problems to the user. Operatives may have to keep returning to their work
over a period of several hours to keep working the mortar to prevent shrinkage and cracking occurring. When using hot lime, as with most types of construction, the weather plays a large part in the final result. It is imperative that the temperature is controlled and the mortar is not exposed to cold or too hot weather conditions. Although the term ‘hot lime’ is used, the hot lime can be used when cold; the term only relates to the mixing process. When the mix has recently been mixed and still retains its heat, it produces a stickier and more pliable mix. The disadvantage is that the batching plant needs to be in close proximity of the work being carried out. The advantage of using the hot mix cold, is that it can be mixed in bulk and transported as required to the area of need.
Quicklime
Quicklime is a limestone that has gone through a chemical reaction in a kiln. The heating of this limestone removes the carbon and moisture, producing the material quicklime. When choosing the aggregate/sand it is imperative to ensure that it comes from a suitable source. It must be free from an excessive number of impurities that could possibly contaminate the mix, resulting in future failure of the hot mix. It is not always possible to obtain a sand that is completely free from impurities, so care must be taken to ensure that the aggregate is suitable to be used. For example, a sand with too high a clay content will result in a necessity to over-slake, which in turn will create a mortar that is prone to excessive shrinkage. There is evidence, however, that a sand containing a small amount of grit and dirt will deliver a mortar of a softer and forgiving nature. But it must be said that the ratio of contaminants must not be excessive. There are two types of quicklime: a finely powdered version and a granular version. The second, known as ‘kibbled’, needs a different mix ratio than the powdered quicklime, as the kibbled is denser before mixing, therefore a different ratio of water and quicklime is required. The kibbled quicklime will also mix and set at a slower rate than the powdered quicklime. This can be an advantage as it is then easier to mix and use. Kibbled lime mortar does not produce as much plume and dust during mixing as the powdered product, therefore the mixing process is not so hazardous to the operative’s health. A disadvantage of using kibbled quicklime is that the granules can sometimes be too disparate, resulting in the heating process during slaking. This can result in contrasting areas of heat within the mix and delayed areas of expansion of the mortar when used.
Case Studies
In the two following case studies, I was appointed as consultant and my company were appointed to carry out the work.
Case Study One
In West Norfolk, there used to be a small village called Appleton, it is believed that this small village could have been a victim of the plague, but no one is really sure why this village disappeared. Where once there was a small community of homes, all that remains is a derelict church. If you were to stand at the top of the church tower on a frosty day, you can see the imprints of where the village buildings stood. The church itself is believed to be a little over 1000 years old, dating back to the time of the Saxons. It also contains reused building materials of Roman origin. Although all that remains is the tower and a few tumbled down walls, this building is still a consecrated church. The church had been left to take on the worst of the Norfolk weather for many years, with very little protection or repairs being carried out. Because of the importance of this church and its association with the royal family, it was decided that this church, with financial help from English Heritage, would be repaired to such a condition that it would be able to withstand any further deterioration.
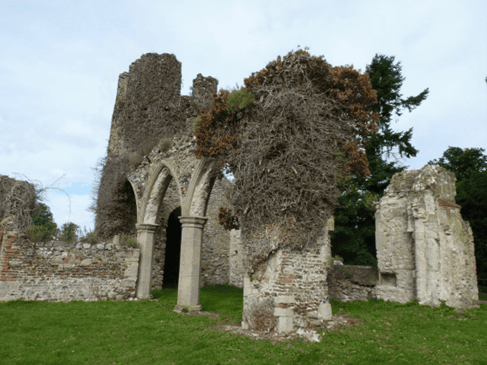
Figure 1: Appleton Church before restoration
A well-respected local architect, with very good experience in working with this type of building, was appointed with the task of saving what was left of Appleton Church. The architect was very keen to repair the building using as many original materials and methods as possible. As much stone as possible was collected from where it had fallen around the building. It was discovered that some of the original stone had been put in storage at a local farm, so this was collected and made ready to be reused.
Several sands were considered to try and match the original sand used during the church’s construction and, after much deliberation, a sand from a local pit a few miles away was chosen. This was a sensible option because when the church was originally built the sand would have been collected locally.
Discussions on the correct lime mortar were had, and the builder was asked to create several small sample batches for inspection. The architect decided on two different types of lime mortar.
An NHL5 mix comprising of 6 of the chosen sand to 1 of hydraulic lime was chosen for any areas that were to be repointed and also for the areas chosen for rough racking, which are exposed areas on top of walls, where stone is bedded to create a top protection of the exposed upper sections of the derelict walls.
For areas of rebuild, a hot lime mixture was chosen, a mixture of quicklime and the chosen sand at a ratio of 5 sand to 1 quicklime. This was to be batched on site and used in its hot state. I believe the reason for the two different mixes was because the architect believed that the NHL5 mix would give better weather resistance to the very exposed tops of the walls. The hot lime would be more suited for the bulk of the rebuilding and repairs, providing a lime mortar that was aesthetically superior, felicitous and more in keeping with the existing structure.
Some areas of the stone building were in such a state of disrepair they had to be photographed, documented carefully, dismantled, and set aside. The idea was (as far as practicable) to rebuild with the removed stones being re-laid in their original positions. The work to the areas of rough racking, using the NHL5 mix, was carried out with little or no problems.
As the majority of this work was carried out in the early part of the year, it was important to ensure that after construction and before the lime mortar set, the tops of the walls were protected from any late frosts, therefore, hessian sacking was used to cover the walls until the lime mortar had set. The rebuilding and repointing element using the hot lime mix was carried out when the weather was a little warmer. This created its own problems; the builders’ operatives had to repeatedly return to their endeavours to rework and repoint the hot lime mix because if it was left, the mortar developed cracks during the drying process. However, the effort put into this process proved to be worth it, as the finished job was very satisfactory.
Now completed, the renovation and repairs to this church should extend its life for many more years. Using carefully chosen materials and original methods has provided a satisfactory outcome, both structurally and aesthetically. The use of lime in the repairs and reconstruction was essential to ensure that the ultimate conclusion met the client’s and English Heritages’ expectations.
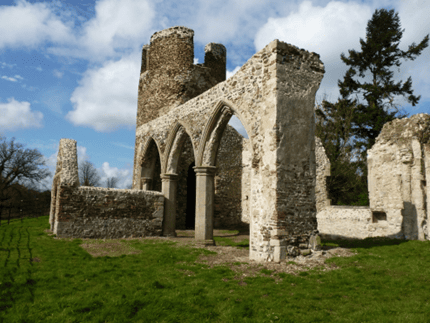
Figure 2: Appleton Church after restoration work
Case Study Two
For 600 years, one of the main roads to enter King’s Lynn in Norfolk has been through the historic South Gate. Where once this narrow arch-like entrance only experienced the traffic of horse carriages and carts, nowadays a high volume of motor vehicles including lorries, pass through this narrow entrance into the town. The interior sides of this magnificent structure are predominantly brickwork. This brickwork and the lime mortar holding it together, has over the last 100 years, seen a huge increase in the amount of pollution and contaminants distributed on to it, affecting its appearance and structural performance.
During the past years, there have been numerous attempts to repair the damage caused by this occurrence. In 2020 it was decided to (once again) carry out a repointing of the worst affected areas. It was discovered that some of the previous repairs had been poorly carried out and even small areas had been repointed using cement mortar. It was believed that the majority of the previous repairs had been executed using an NHL3.5 lime mortar mix. It was considered that perhaps an NHL5 lime mortar mix may be a better solution to resist the attack from traffic pollution. The works needed to be carried out at the quietest times to lessen the disruption to traffic through this busy thoroughfare. Therefore, it was decided to carry out the works during late night and early mornings to reduce the problem.
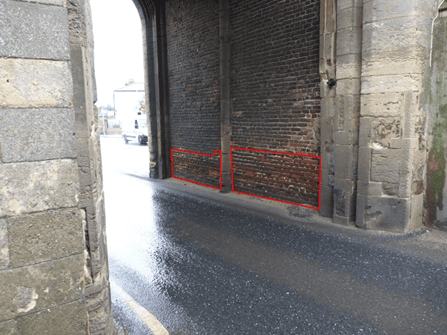
Figure 3: The South Gate, areas showing deterioration before repointing works
The worst areas of affected mortar joints were carefully cut out to a depth of around 25mm, however, some areas had already deteriorated to this depth and beyond, and the joints only required cleaning. A gritty sand was chosen and an NHL5 lime. The joints were then carefully repointed and finished with a wooden pointer.
On revisiting this project nearly two years later, it can be seen that even the repointed mortar joints are beginning to show, once again, the effects of the traffic pollution, with some areas almost back to their 2020 condition. Although repointing in cement mortar, was not an option for obvious reasons, this may have fared better than the lime mortar, with more resistance to traffic pollution. But even if allowed, the use of cement would have created its own problems with this historic building. There are now discussions taking place considering an alternative road layout, to avoid traffic passing through this ancient gateway. If this comes to fruition, then I believe that this could be the best solution to preserve The South Gate for the future.
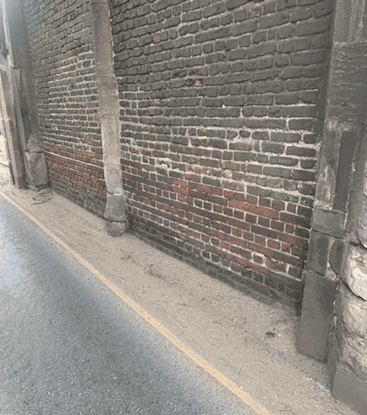
Figure 4: The South Gate, same areas showing partial deterioration, two years after repointing
Conclusion
I have discussed the use of lime mortars and their use from an early date and how they have contributed to so many historic buildings. The material allowed bigger and stronger buildings to be constructed, even in some of the most extreme conditions, such as the Eddystone Lighthouse. Lime mortars have been continually used to some degree for hundreds of years, being basically the only reliable medium for bonding building materials together. With the introduction of cement mortars, the use of lime mortars became relegated mostly to the repair and reconstruction of older buildings. However, lime mortars seem to be gaining popularity again, with some designers and builders preferring their use over cement mortars. Mainstream builders of large developments still mainly use cement mortars, mainly for cost and convenience, but many new construction projects are taking place with the use of lime mortar. More control is required with the mixing and conditions of use, therefore, it takes a greater degree of supervision and care, something that is not always possible or provided on large development projects. There is a place in construction for both lime mortars and cement mortars, and designers and architects will decide on what is the most suitable for their projects. In my view, the use of lime mortars will always be part of future construction, either with new projects or repairing the old.
Sources
Buildingconservation.com
Graymont History of lime and mortar.
Archives and research, Lime mortars in Traditional Buildings.
ACADEMIA History of lime mortar
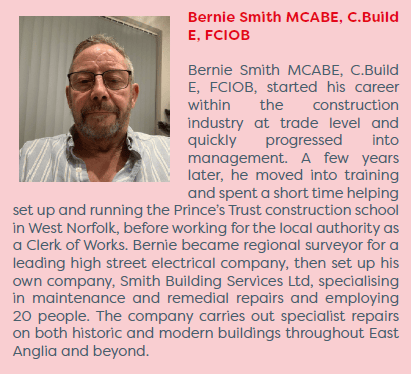