Older PVCu Replacement Windows.
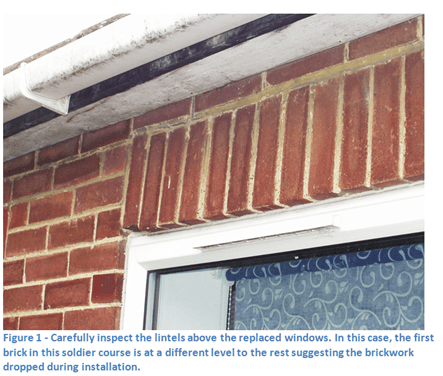
Remember when PVC replacement windows became all the rage? Along with stick-on stone cladding, double-glazed replacement windows quickly became the ‘must have’ feature for home owners in the late 1970s and the early 1980s. As ‘right to buy’ policies flourished, one of the best ways to show the world “we no longer lived in a council house” was to install double glazing – it became a status symbol.
However, a quarter of a century before replacement windows where first controlled by the building regulation, early standards were variable. Gaskets failed, double glazed units misted over and insecure beads and other PVC components became brittle and in many cases, were unrepairable.
Following a number of complaints against surveyors about their assessment of older PVC windows, this article will establish a number of ‘benchmarks’ against which these windows can be assessed no matter what their age.
For reasons of brevity, this paper concentrates on assessing the condition of replacement PVCu windows only. PVCu doors will be considered in a future bulletin.
Inspecting windows
The first step is to make sure you are carrying out the right level of inspection and collecting the appropriate information. This will depend on the specific terms and conditions you have agreed with the client. Rather than going through each variation, I think RICS’s Guidance Note ‘Surveys of Residential Property’ (SORP) sets out a practical approach. It identifies three different levels of inspection:
- Survey level one (for example, a condition report) – you should attempt to open only a limited sample of the windows and this might typically include one on each elevation and especially on the most weather-exposed side.
- Survey level two (for example, RICS HomeBuyer and SAVA HCS) – you should attempt to open a representative sample of the windows. For example, this might include one on each elevation (as above) and one of each different type of window where there is a variety.
- Survey level three (for example, RICS building survey) – you should attempt to open the majority of windows where possible.
This may help set the standard approach but the reality is never straight-forward. For example:
- In all cases, you should only open windows where the occupier has given their permission; and
- Where keys are available and the locks are easy to operate without force or damage.
Often window sills cluttered with possessions and heavy curtains will make it difficult to inspect the windows. In these cases, you will have to make your own decisions but I would suggest on levels one and two inspections you should not move anything. For level three, I think a small amount of possessions/curtains should be repositioned. Another way of tackling this is to ask the occupant to clear the sills from the windows you want to inspect.
From the outside, you should carry out a visual inspection of all window frames using your binoculars where appropriate.
Where your inspection is restricted, you MUST clearly tell your client in the report and outline the implications of the restrictions.
Assessment ‘benchmarks’
Although replacement windows were not covered by the building regulations until April 2002, the current regulations provide a very useful framework against which all installations can be assessed. Clearly pre-2002 windows will not match the more exacting 2017 standards so you will need to use your professional judgement.
The Building Regulations
In April 2002, replacement windows and doors came under the control of the building regulations. You should ask the vendors for evidence that any replacements installed after that date complies with the appropriate standards. There are two ways of showing this:
- Certification showing that the work has been done by an installer who is registered under an appropriate competent person scheme. The Fenestration Self-Assessment Scheme (FENSA) is probably the most common (with over 7 million registrations) but other suitable schemes now include BM Trada Certification, the British Standards Institution, CERTASS or Network VEKA.
- Certification (usually a final completion certificate) from the local authority confirming that the installation has approval under the Building Regulations.
Because of the growing number of competent persons schemes, rather than simply using ‘FENSA’ in your reports, consider using a phrase like:
‘The windows should have been installed by an organisation who is a member of a government approved competent person scheme. Follow this link for more information:
(https://www.gov.uk/building-regulations-competent-person-schemes)
However, your job doesn’t finish there.
Checking the key indicators
Even if the vendor thrusts a certificate in your face, you should still check the installation for any obvious signs of non-compliance. The main ones are described below and are loosely group under different parts of the Building Regulations:
Structural support (Approved document A)
In my experience, many window installers have worked on the assumption that gravity is slow. As long as they got the old windows out and the new ones installed quickly enough then they didn’t have to worry about temporary structural support. The amount of cracking and structural movement above and around replaced windows suggests to me that gravity may be quicker than first thought!
On a more serious note, this is one of the more important factors because many original window frames had an informal load bearing function. If this wasn’t properly recognised and accommodated in the design and the replacement process, localised damage could occur.
The responsibilities for this are clear. For example, the Glass and Glazing Federation (GGF) state that if no lintel is fitted above the existing opening, the installation company is responsible for assessing if one is required. The installer cannot avoid the issue on the grounds that because the original window did not have a lintel, then the replacement does not need one either. In such a case, there are two options:
· The installer should recommend a new lintel is required (usually fitted by others); or
· The new window frame is designed to be load bearing. For example, most PVC windows incorporate a reinforcing steel frame and these can be very strong.
It is not only the nature of the opening and the strength of the window that is important but also the level of temporary support provided during the replacement works. If these are insufficient (or non-existent) then structural damage could occur.
Bay windows are particularly vulnerable as the lower windows will often support loads from above including the bay walls, part of the first floor and sometimes the flat roof over the bay itself.
In all of these cases, it is vital you look for signs of movement including:
- external and internal cracking;
- sloping floors within the bay at first floor; and
- Distorted openings where the opening casements stick or do not open at all.
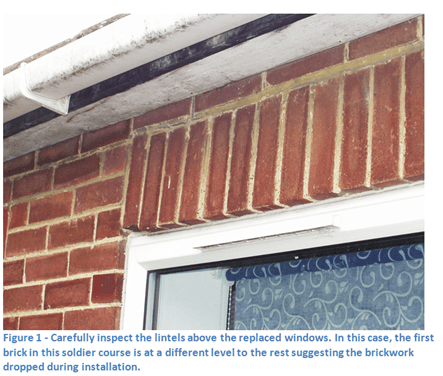
Means of escape (Part B):
Most building control departments will strongly advise that all first floor windows in dwellings should have opening lights/casements large enough to allow occupants to escape if trapped in the room by a fire. Usually the opening part of the window should have an unobstructed open area of at least 0.33m2, be not less than 450mm high and 450mm wide and not more than 1100mm off the floor level. However, the route through the window may be at an angle rather than straight through.
This also applies to ground floor rooms that do not open directly into a hall leading to an external door. An ‘inner room’ is a typical example.
Sadly, all of this is not a strict requirement of the building regulations. As long as the installer did not make matters worse (for example, make the opening windows smaller than the originals) then the installation could still get its competent person’s certificate but have windows through which the occupants could not escape. In these cases, you need to clearly warn the client of the potential risks.
Upper floors more than 4.5m above ground level (say second floor and above) should be accessed by a “protected stairway” or an alternative escape route and so fire escape windows are not required at this level.
Other indicators you may want to look out for:
- Windows (particularly top opening casements and roof windows) should be designed to remain open without needing to be held by a person making their escape.
- Many pivot type windows do not have an unobstructed open area suitable for escape purposes.
- Locks (with or without removable keys) and stays may be fitted to egress windows, subject to the stay being fitted with a release catch, which may be child resistant.
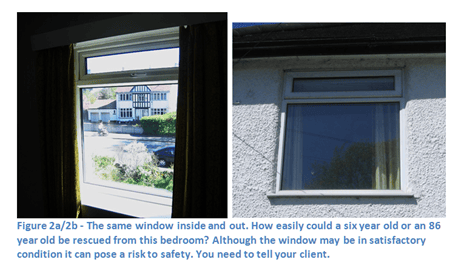
If you are carrying out an HCS, the SAVA protocol is clear when means of escape do not meet current standards. The surveyor applies their judgement according to the scale of the remedy.
The hazard must be flagged up in Section C of the report.
Ventilation (Approved document F – Means of Ventilation)
As with other provisions, the replacement windows should not make matters worse. So if the original windows did not have fixed ventilation (for example, trickle vents) the new ones don’t have to have them either. However, building control authorities will encourage the use of trickle vents but cannot force the matter.
Consequently, to keep costs down many installers will not offer tickle vents as standard but as an additional feature for which there is often a cost. Some installers will argue that windows can be locked in a ‘crack ventilation’ position but my experience suggests most occupiers are reluctant to leave their windows open especially when they are out.
This lack of trickle ventilators can result in increased levels of condensation after the new windows have been fitted. This is because informal ‘adventitious’ ventilation provided by the old draughty windows is dramatically reduced.
Where trickle ventilators have not been fitted these can often be fitted retrospectively by either:
- cutting/drilling through the frame and fitting appropriate ventilators either side; or
- By replacing a glazed panel so a slot ventilator can be fitted across the top of the new glazed unit.
Other points to watch out for:
- Particular care should be taken when the room is fitted with a gas cooker or other flueless appliances (for example, a water or space heater). The window installer should have referred the matter to a “Gas Safe” registered gas engineer for advice but if you are worried the room may now be too tightly sealed, check to see if the gas appliance has been checked/serviced since the replacement window was fitted. If not, then an urgent further investigation may be required for safety reasons; If the windows have been replaced as part of a material change of use (for example, conversion of a house into flats) then the window must comply with the full Building Regulations requirement for windows in new buildings.
Note, for the HCS even if a Gas Safe Certificate is available for you to check and is current, if the windows have been installed since it was issued you should still issue a CR3 if you believe lack of ventilation could impact on health and safety of the occupants. You should explain this in your justification for a CR3.
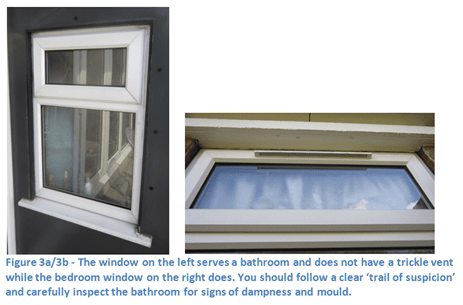
Glass safety and critical locations (Approved document K)
During your inspection, you should look out for glazing in ‘critical locations’ (see figure 4). In these positions, the glass should either:
- Break safely. When broken, the glass should not be capable of causing injury. The Glass and Glazing Federation give advice on the different markings manufacturers use to show compliance. In my view, we should not bother trying to decipher any symbols we see. Simply look for some sort of permanent marking on the glass (these will usually be in one the bottom corners of the panes). If there is no mark then the client needs to be warned (see figure 5).
- Be robust. Some types of glass increase in strength with thickness (for example, annealed glass) but this is difficult to assess on normal surveys both in terms of the type of glass and its thickness (see the discussion on the use of laser measuring gauges).
- Be in small panes. Glass in small panes will be less likely to cause injury. The panes should be a maximum of 250mm wide and not exceed 0.5m2 in size.
- Be permanently protected. If the glazing in the critical location is protected by a permanent screen then the type of glass is not an issue. The screen should be robust, not easily climbed (no horizontal rails) and prevent a 75mm sphere from coming into contact with the glass (note: smaller size than for balustrades).
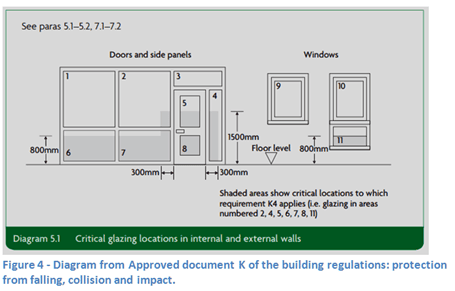
In bathroom areas where the window is situated adjacent to the bath/shower, the finished floor level is taken from the bottom of the bath or shower cubicle and not the floor level where the bath or shower has been installed.
Most building control authorities recommend that window restrictors are always fitted to opening lights/casements less than 800mm above floor level.
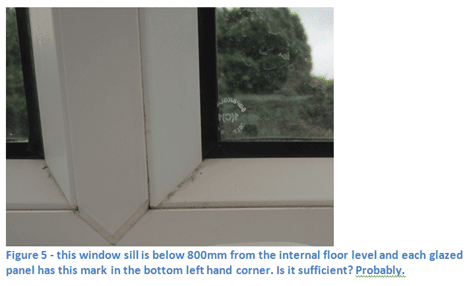
Conservation of fuel and power (Part L)
In my opinion, you should not be asking for separate evidence that shows the window complies with Part L but familiarity with the relatively new Window Energy Rating system (WER) will be useful.
The British Fenestration Rating Council (BFRC) Scheme is the UK’s national system for rating the energy efficiency of windows and is recognised within the Building Regulations and competent person schemes as a method to show compliance.
The WER is an objective method used to assess the total energy performance of a window and it takes into account:
- The materials used (glass, framing materials and so on);
- The air leakage (through gaskets and joints but not the junction between the frame and the wall); and
- The solar gain (energy from the sun).
The scheme puts the window type into a rated band (A to G). It uses standard size windows and so provides a simple method of comparing different products from either the same or different suppliers. A typical WER certificate (see figure 6) includes the following information:
- The band rating of the window. Band C is the minimum for building regulations compliance.
- The energy efficiency rating – a negative value represents an overall heat loss. A zero or positive value indicates an overall contribution to the heat levels in the home. In other words, a window with a positive value gains more heat from the sun than it loses from the room.
- Details on the factors that affect the rating such as the U value (thermal transmittance), how ‘leaky’ the window (air leakage) is and an allowance for solar gain (solar factor).
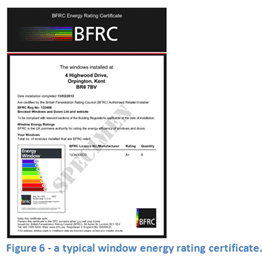
Although there are a number of different ways of achieving this standard, you should be looking for double glazed units that are wider (say 16mm and more). Personally, I don’t think you should be looking for reference numbers printed onto the silver spacers between the panes, just take a broad view. The older the windows, the lower the thermal efficiency it is likely to be.
Laser glass measuring gauges – should I use them on an inspection?
Laser glass measuring gauges are available and many of these are able to measure the thickness of the glass, the width of the air gap and even whether the glass panes are laminated. Although relatively inexpensive and easy to use, I would advise against using them on Level one and two products. This is because this level of analysis goes well beyond the terms and conditions of most survey products. Additionally, these gauges will only give a partial assessment of the window. It can’t detect whether the panels are argon filled or have low emissivity coatings and so on. Like all of our tools, they must be used wisely.
Security (Approved document Q: Security – Dwellings)
This is the new kid on the block and only applies to new dwellings since 2015. Like most modern approved documents it is very brief and apart from stating some broad performance standards, it refers to other documents that described the requirements in more detail.
Approved document Q refers to ‘easily accessible’ doors and windows that give access:
- to a dwelling from the outside;
- into parts of a building containing flats from the outside;
- Into the common parts of a building.
To meet the requirements of Part Q, the windows have to resist physical attack by a casual or opportunistic burglar by being robust and fitted with appropriate hardware. One way of showing this is by ensuring the windows have been made to the security requirements of British Standards publication PAS 24:2012. What are the security requirements of PAS 24? To be honest, I haven’t the faintest idea as this goes beyond the level of knowledge required for most condition surveys. In my view, it is reasonable to assume replacement windows covered by a competent person scheme or a building regulation approval should meet with these new requirements.
External beads – a security risk?
Older installations often have the glazing beads positioned on the outside of the glass. Although this allowed the glazing to be replaced with little or no disturbance internally, it also proved very popular with burglars who could take the beads and panels out within seconds! Therefore although external beading by itself does not automatically condemn the installation it certainly will be a major consideration.
Other factors that may influence the assessment
Although not part of the formal regulatory framework, there are other features of window replacements that are becoming important.
Air-tight perimeter seals
The original purpose of perimeter sealants between the frame and wall was to repel water but as energy efficiency requirements have tightened, preventing heat loss through air leakage between the frame and the structural opening has become more important. This is more than a bit of expanding foam squirted in the gaps or a poorly applied mastic seal on the outside face. It should involve the use of appropriate gap filling materials, air tight tapes and other techniques. As you might imagine, not all installers follow rigorous quality assurance processes so the following pointers may be useful:
- This becomes more important for dwellings at the higher end of thermal performance (Passivhaus for example);
- Look for obvious signs of poor workmanship. A typical example would be poorly applied mastic on the outside; and
- Check carefully around the inside junction of the frame and the reveals for signs of air leakage. In the worst cases, this can show up as ‘dust streaking’ to the decorative surface.
The problems with spacer bars
Spacer bars are the continuous hollow frames which separate the two glass panes in the double glazed panels. The bar is bonded to the glass panes by a primary and secondary seal, creating an airtight cavity which is filled with air or gas. The spacer bar itself is filled with a desiccant to absorb any residual moisture within the cavity and thus prevent condensation within the double glazing window.
Spacer bars are an important contributor to a window’s energy ratings. They are typically made of aluminium, or a low heat-conductive material (known as a warm-edge spacer).
There are a number of problems associated with spacer bars:
- If the primary and secondary seals between the glass and the spacer breakdown, the sealed unit will be vulnerable to misting between the glazing panels. Once this has occurred, the sealed unit will have to be replaced; there are no repair options. In terms of longevity, most commentators suggest that spacers that sit within windows rebates that are drained and ventilating (for example, most PVC frames) will last longer than those that are in undrained rebates (for example, many timber windows).
- Spacers act as ‘cold bridges’ and allow heat to conduct from the inside to the outside at a greater rate than the adjacent frame and glass (although modern spacers use ‘warm edge technology’ to reduce this effect). Where there is a cold bridging problem, older replacement windows can show a thin line of condensation just above the internal beading (see figure 7).
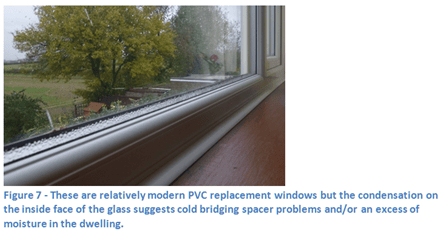
General condition
An internet search for any town or city will identify a number of organisations specialising in repairs to PVC windows and doors. Ranging from hinge and lock repairs, replacement of defective gaskets to the repair of cracked and scratched PVC components, contractors will rightly claim to be able to extend the economic life of older PVC windows.
However, the older the installation the more difficult it will be to get replacement parts. Like all maintenance activities, there will be point where the level of performance and the cost of repair may justify the window’s replacement especially when considered over the medium term.
Accurately identifying this point goes beyond the scope of most survey products. Despite this, it may be possible to put the client into the right ‘Ball Park’. Assuming you have carried an appropriate inspection, the overall condition of the installation will be a function of the following factors. For example:
- Are all the gaskets and seals in place? Are there any missing? Have some shrunk back from the corners? (see figure 8).
- Are the seals brittle/inflexible? This will result in draughts.
- Are the mitred junctions between the different parts of the casements/frame members properly sealed or have gaps appeared (see figure 9)?
- Are the windows easy to open? Do the casements catch against their frames? Are the hinges and stays rusty/distorted?
- Do the handles operate smoothly? Are they robust? Are they loose?
- Is it easy to lock/unlock the casements?
- Are the PVC surfaces of the frame and casements scratched, fractured or broken? If yes, can they be easily repaired?
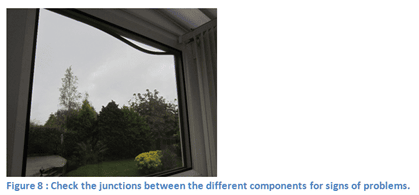
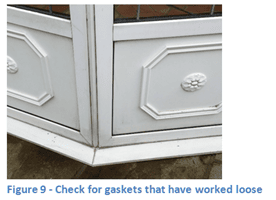
Assuming you may have only opened and closed 25 – 30% of the windows in the dwelling, it is not be possible to be prescriptive as to what level of defects and/or deficiencies equate to the ‘end of the installation’s economic life’. I try and imagine what how the three condition ratings relate to the magnitude of the defects I see during the inspection:
Condition rating 1 – No observed defects
Condition rating 2 – although there are a number of problems that need repairing, none of these are urgent or prevent the windows from fulfilling their function.
Condition rating 3 – there are a number of problems and some of these are urgent (for instance, the window is insecure, it is allowing water to get in or parts are likely to fall out) or serious (there are so many smaller repairs that the window now needs replacing).
As with the general assessment protocol described below, it is difficult to give accurate outcomes. All we can do is review the information we have collected during the inspection and come to a suitable condition rating decision.
If you are doing a Home Condition Survey remember – the use of the SAVA Protocol in the Product Rules is mandatory when assessing a condition rating. You still apply your professional judgement – but in a structured way and in fact, would coincide with the thought process of the author.
The BlueBox/SAVA assessment protocol for replacement PVCu windows
Not another one we hear you say! Stick with me. Like many of the protocols created before, this is not intended to replace your own decision making but to support it (and help you answer the questions raised in the ‘Boxes’ if you are completing and HCS).
Once you have collected the data on site, respond to this series of questions. The answers may help you reflect on the outcomes of your inspection and arrive at a confident decision.
How to use the protocol
The questions are designed to illicit ‘yes’ or ‘no’ answers. Simply pose the questions, tick the appropriate box and when complete, stand back and look at the mix of the answers. If there are more ‘yes’ responses then it could suggest a condition rating one or two. More ‘no’ answers could indicate a condition rating two or three. However, watch out for the exceptions. For example:
- Although the process may produce a clear majority of ‘yes’ responses, some of the safety issues (for example, a low sill with unprotected glass) may be so dangerous you may want to allocate a CR3 (For an HCS you probably will!) ;
- The rule governing ‘further investigations’ will always apply. If you recommend an aspect of the installation needs to be examined further then a CR3 will be appropriate whatever the mix of responses.
YES | ASSESSMENT FACTOR | NO |
Were the windows installed after 2002? | ||
If you answered yes to the question above, have you seen evidence of a competent person’s scheme or building regulation approval that covers the whole installation? | ||
Are the structural openings of the replaced windows free from signs of building movement? | ||
If a fire was to trap you within any of the habitable rooms, would you be able to get out through an opening casement? | ||
Are any parts of the windows less than 800m from the internal floor level? | ||
If you answered yes to the question above, are the lowest parts of the glass properly protected against breaking? | ||
Are there signs of water penetration on the inside of the window frame (especially under the sill)? | ||
Is the gap between the glass panes closer to 16mm than 6mm? | ||
Are the glazing beads on the inside? | ||
Are the windows in a generally satisfactory condition (seals, splits, hinges, locks and so on)? |
Sample phrases
These would be suitable for level 2 products.
These are in no particular order and please make sure these are adapted to suit your own particular situations.
Replacement windows
The windows are a mixture of (describe the original and new window types).
Condition rating 1. No repair is currently needed.
The property must be maintained in the normal way. You should ask your legal adviser to check whether the replacement windows have either building regulation approval or have been installed by a contractor registered with the Government’s Competent Person’s scheme (see section I2[HBR]/see section C[HCS]).
If there is no evidence, you should ask an appropriately qualified person to inspect the windows and check their suitability.
No fire escape window
For a Homebuyer Report:
The design of the original/replacement windows does not allow people to escape from a fire (describe location and nature of problem). This is a safety hazard (see section J3 Risks).
Condition rating 1 – No repair is currently needed. The property must be maintained in the normal way. To reduce this hazard, you should ask an appropriately qualified person for advice.
For an HCS:
The design of the original/replacement windows does not allow people to escape from a fire (describe location and nature of problem). This is a safety hazard (see section C Risks to People).
Condition rating 3 – No repair is currently needed but I have allocated a CR3 because, although compliant with regulations at the time that they were installed, in the event of a fire, they would seriously impede escape from the property.
[Note: if some windows were compliant and some were not, in an HCS it would be acceptable to apply different Condition Ratings to different groups of windows or even to a single, non compliant window. ]
No safety glazing
For a Homebuyer Report
The glazing to the low level window (describe location) is unlikely to be safety glass and will be a safety hazard for anyone who falls against it. This is a safety hazard (see section J3 Risks).
Condition rating 1 – No repair is currently needed. The property must be maintained in the normal way.
To reduce this hazard, you should ask an appropriately qualified person for advice.
The opening windows are not fitted with restrictors and so do not have protection from the danger of falling (see J3).
For an HCS
Refer to box B and C on the SAVA Protocol. You will attribute a condition rating depending on ‘the scale of the remedy’ and the Risk. This is likely to depend on the location of the offending window/glazing and you would attribute a CR 1, 2 or 3 depending on the level of risk
Misted units
The double glazing units (describe location) have failed and the space between the glass panes has ‘misted’ over.
Condition rating 2 – This is not a serious defect but is unsightly and can reduce the thermal efficiency of the double glazing. You should replace this/these soon.
Where some double glazed panels have failed, the remainder could suffer similar problems and you should plan to replace more in the near future. It can be difficult to replace just the double glazed units on some older windows. In these cases, you may have to plan to replace the whole window.
Older PVC windows
The windows are doubled glazed with PVC frames are likely to be original to the property.
Condition rating 1 – No repair is currently needed. The property must be maintained in the normal way.
Although I did not see any problems in the sample I opened, these windows were installed before 2002 when the tighter regulations were introduced and are unlikely to be covered by a guarantee/warranty. The cost of maintaining older PVC windows can increase with age.
The windows are doubled glazed with PVC frames are likely to be original to the property. A number of double glazed units have misted over and several seals/gaskets are defective/poorly fixed.
Condition rating 2 – I saw a number of problems in the sample of windows I opened. You should ask an appropriately qualified person to inspect all the windows and provide you with a report together with quotations for repair. Although the extent of these repairs will not be known until this report has been received, you should plan for a major overhaul of the windows.
These windows were installed before 2002 when the tighter regulations were introduced and are unlikely to be covered by a guarantee/warranty.
The cost of maintaining older PVC windows can increase with age.
Extract from SAVA Product Rules (V10) Page 20 (vi) Windows (a) Include shutters and shutter furniture and security fixtures and locks if they exist (b) Inspection: upper windows will normally be viewed from ground level using binoculars, though if an opportunity exists to view higher levels from other vantage points this should be taken wherever possible, the inspection should be from all sides, noting that the inspection should only be from the property itself and any adjoining land to which the public has access access limitations which could add to repair costs should be noted and should be considered when determining if a Condition Rating 3 is appropriate inspect external surrounds, i.e. lintels, cills, jambs as well as frames and glazing inside, open and close a sample of windows to test that they work properly test for damp around window openings |