The Fundamentals of Passivhaus.
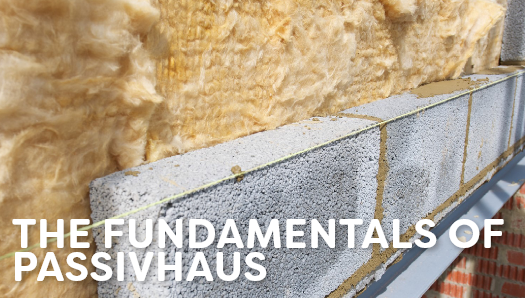
Samuel Lott, BSc (Hons) MSc, Data Consultant (Energy), Sava
Dr Neil Cutland MInstP, Special Projects Director, Sava
In this article, Sam Lott and Neil Cutland explain the fundamentals of Passivhaus. This article is an extract from the NHBC Foundation report titled ‘The UK’s progress towards a Passivhaus standard in new homes’ which was researched and written for the Foundation by Sam and Neil, and is downloadable here.
What is Passivhaus?
Passivhaus is an energy-efficient building design and construction concept that originated in Germany in the late 1980s. The concept is owned by the Passivhaus Institut of Darmstadt, Germany, which strictly regulates the certification of buildings and ensures that high-quality standards are upheld.
The fundamental principle behind Passivhaus is to create structures that minimise the need for active heating or cooling systems. By utilising a combination of design strategies and high-quality building materials, Passivhaus buildings aim to maintain a comfortable indoor environment while significantly reducing energy consumption. By definition, they focus on design features that are passive in functionality such as insulation, airtightness, and solar orientation. However, they also include active elements in design to ensure comfort for residents, most notably mechanical ventilation systems with heat recovery (MVHR). The overall aim of Passivhaus is to eliminate the need for traditional wet central heating systems. This is achieved by reducing the space heating load to a level where the required heat can be provided via the ventilation air alone.
The requirements of Passivhaus
Passivhaus requires a building to conform to strict requirements in order to be deemed Passivhaus compliant and achieve certification [1]. These requirements are as follows:
1. The space heating demand of the building is not to exceed 15kWh per year per square metre of net living space (treated floor area), or 10W per square metre peak demand. In climates where active cooling is needed, the space cooling energy demand
requirement roughly matches the heat demand requirements above, with an additional allowance for dehumidification.
2. The Primary Energy Renewable demand (PER) for all domestic applications (heating, hot water, and domestic electricity) must not
exceed 60kWh per square metre of treated floor area per year. [2]
3. The property must meet airtightness limits with a maximum of 0.6 air changes per hour at 50 Pascals pressure, as verified with
several onsite pressure tests (in both pressurised and depressurised states).
4. Thermal comfort must be met for all living areas during winter as well as in summer, with the internal temperature not exceeding
25oC for a maximum of 10% of the hours in a year.
5. Requirement to record/photograph certain construction stages.

Table 1: Requirements of Passivhaus Plus and Premium
Passivhaus also offers a Passivhaus Plus and Passivhaus Premium standard, both of which incorporate the use of renewable energy generation in the certification assessment.
The PER demand focuses on the portion of primary energy use that is derived from renewable energy sources and is a subset of the total primary energy use.
The Passivhaus principles
In order to meet the rigorous standards of Passivhaus, intelligent design is imperative to reduce air leakage in the building and also meet the space heating demand target. There are, therefore, five key basic principles that apply to the construction of a Passivhaus building:
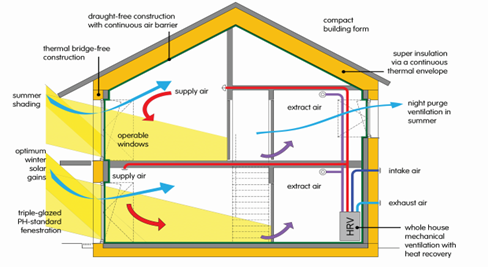
Figure 1: Passivhaus Principles
Thermal insulation
One of the basic principles of Passivhaus design is a well-insulated building envelope. Typically wall, roof and floor elements will achieve a U-value of between 0.10 W/m²K to 0.15 W/m²K [3]. They will also achieve minimal thermal bridging and, in some construction types, provide an internal service void so that services do not penetrate the airtight barrier of the building. This internal service void is important as it means that once the building has been constructed there should be no need to disturb the envelope of the building hence disrupting the airtight membrane that has been installed. This allows for easier repairs from within the internal service void.
Passivhaus walls are generally thicker, varying from 300mm to 500mm depending on the construction method and insulation chosen.
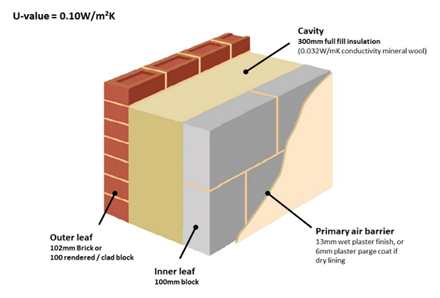
Figure 2a: cavity wall build-up of a Passivhaus (H + H UK Ltd)
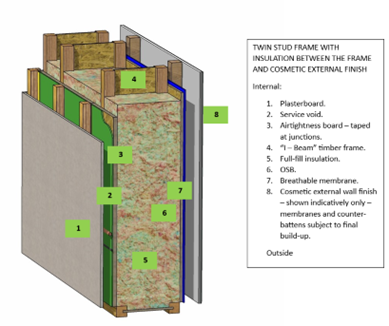
Figure 2b: timber frame wall build-up of a Passivhaus (Credit: Alan Budden, Eco Design Consultants)
Floors are often constructed from insulated slabs which allow for a continuous insulated area with no thermal bridging and complete airtightness. There are instances where beam and block construction are used, although, this often requires adaptation and extra insulation to ensure it meets the U-values required for Passivhaus.
Well-insulated roof systems also play a crucial role in regulating indoor temperatures, helping to keep homes warm in the winter and cool in the summer.
Thermal bridge reduced design
Thermal bridging, also termed cold bridging, denotes localised regions within a building’s envelope where the insulation barrier is compromised, permitting an easier flow of heat compared to the surrounding materials. Essentially, thermal bridging represents a path of heightened heat conductivity that circumvents the insulation layer, resulting in an increased heat transfer zone between the building’s interior and exterior.
Neglected thermal bridges can escalate heat loss from the building’s structure by over 30%, primarily stemming from materials such as concrete or metal components, thereby impacting thermal comfort and potentially causing condensation.
Common instances of thermal bridges encompass structural components such as beams, columns, and studs in walls or floors, alongside areas surrounding openings like windows, doors, and vents. During cold weather, these zones may experience lower temperatures compared to the remainder of the building envelope, leading to heat dissipation, potential condensation, and occupant discomfort. In Passivhaus design, a strategic approach is adopted to eradicate thermal bridges through the incorporation of thermal breaks at vulnerable junctions, such as where steels connect to a concrete floor, ensuring optimal insulation continuity.
High-performance windows
Windows used in Passivhaus are designed to meet the strict energy efficiency and comfort standards of the Passivhaus standard. They achieve this by incorporating insulating frames with thermal breaks and typically triple glazing with low-emissivity coatings and gas filling.
Windows are sealed tightly to prevent uncontrolled air leakage. This involves using high-quality gaskets and sealing materials. They are also strategically sized and positioned to balance daylighting, solar gain, and thermal performance.
Solar control is achieved by positioning windows to optimise solar heat gain during the winter and incorporating shading devices to minimise heat gain during the summer [4].
Airtight construction
Ensuring airtightness is crucial to the fundamental principles of Passivhaus. This is achieved through the use of a continuous air barrier that envelopes the entire structure, from walls and roofs to floors and openings.
The design process identifies all potential air leakage paths and emphasises the sealing of joints and connections. The use of high-quality building materials including tapes and membranes ensures the airtightness of the building.
A breather membrane is often added externally, along with an airtight barrier which can be plywood, OSB, plasterboard or a flexible membrane. The airtight barrier is then sealed with specialised tape [5]. In masonry construction, the required airtightness is sometimes achieved using plaster alone.
Blower door testing is conducted to measure the buildings’ air changes per hour under pressure. The maximum permitted is 0.6 ACH @ 50 Pa. Chemical smoke, thermographic cameras and anemometers may be used to search for leaks, which can then be plugged.
Airtightness – understanding the units
Passivhaus measures the outcome of a pressure test in terms of air changes per hour (ACH), representing how many times the entire house volume is replaced with air in an hour, at a pressure differential of 50 Pascals (Pa). Conversely, UK Building Regulations quantify airtightness by calculating the absolute volume of air replaced per hour divided by the total external envelope area under the same pressure differential of 50 Pa (for blower door tests). The units in this case are m3/m2h. Achieving an accurate conversion from one system to the other hinges on the building’s size and the area-to-volume ratio. As a rough estimation, the 0.6 ACH of the Passivhaus standard is approximately equivalent to 1.0 m3/m2h in the UK terminology (at 50 Pascals in both cases).
Adequate ventilation strategy
With the building now sealed for airtightness and minimal air leakage, the focus shifts to ensuring proper ventilation to keep the indoor air fresh. Stale air is removed from the building and passed through a mechanical ventilation system with heat recovery (MVHR). Here the heat is recovered from the stale air and transferred to the incoming fresh air. Passivhaus MVHR systems have heat recovery efficiencies ranging from 75% to 95%, with 75% being the minimum to meet Passivhaus requirements. The incoming and outgoing airstreams mustn’t be allowed to mix, to avoid contamination between the two.
The Passivhaus Planning Package
In order to meet Passivhaus standards it is important to use a certified Passivhaus designer, architect, or consultant. In the UK such practitioners can be found on the Passivhaus Trust “members map” [6]. A Passivhaus designer will use the Passivhaus Planning Package software (PHPP) which will calculate the key parameters from the design plans and explore options for compliance and give recommendations for achieving the Passivhaus standard.
SAP or PHPP?
The Passivhaus Planning Package (PHPP) is an energy calculation tool based on an Excel spreadsheet developed by the Passivhaus Institut in Germany. The Institut exclusively authorises the simulation and certification of operational efficiency for proposed Passivhaus constructions. While PHPP shares energy calculation techniques common across Europe, like the UK’s SAP, it also includes other factors such as household appliances. Moreover, it offers a deeper analysis of certain aspects of the computation, for example, thermal bridging. Research conducted by the Passivhaus Trust, the Association for Environment Conscious Building (AECB) and Elmhurst Energy into PHPP and SAP concluded that the core of both models was very similar. However, the models are used for very different purposes.
SAP is a more standardised calculation tool used as a method of compliance. Its primary focus is to establish consistent regulations across the UK, potentially at the expense of precise data. As a result, SAP employs average UK weather data, which means that dwellings in colder regions do not necessitate extra insulation for compliance. PHPP on the other hand, always uses local climate data and includes further details in certain sections such as the calculation of shading for individual windows.
The key difference between the two models is how they are employed, rather than the accuracy of the models themselves. In essence, the underlying physics of the two methodologies give very similar energy results, but PHPP uses more precise data which can reduce the performance gap.
At the time of writing the UK Government is consulting on a replacement for SAP. This is currently referred to as the Home Energy Model (HEM) and is looking to make the calculations more accurate [7]. The core of the model will calculate the energy requirements of a dwelling in a similar fashion to SAP/PHPP: this will then be overlaid with ‘wrappers’, which will apply further steps in the calculation process to determine metrics associated with meeting the Future Homes Standard. Part of the validation process of this new model is comparing with outputs from the PHPP tool.
The performance gap
The performance gap refers to the disparity between the anticipated energy efficiency and performance of a building as initially predicted during the design and simulation stages, versus the actual energy performance observed during its operational phase [8]. This discrepancy can arise due to factors such as construction quality, occupancy behaviour, system operation, or inaccurate assumptions in modelling. Studies have conducted post-occupancy evaluations and found energy consumption can be many times higher than compliance calculations made during design. This highlights the need for better alignment between design expectations and real-world outcomes to achieve intended sustainability and efficiency goals.
Passivhaus certification
The Passivhaus Institut has developed a quality assurance certification process to prevent false claims and abuse of the term ‘Passivhaus’. The Passivhaus standard is based purely on building physics and the criteria for certification are performance-based, instead of relating to individual construction or technical details.
For certification to be granted, a building must first undergo modelling in the PHPP where checks are made to ensure the building complies with all criteria. This is the initial check, and if at any point it fails, recommendations are given to assist the designer in achieving compliance. Once an initial review has been done the design then goes through full PHPP verification. This is where designers will refine construction and select products to ensure compliance.
During the construction phase of a Passivhaus project, it is advised that Certified Passivhaus Tradespersons are used who are trained in the principles to ensure the correct implementation of the design [9]. Quality assurance measures are applied throughout construction, such as multiple pressure tests, detailed documentation of the MVHR commissioning, and photographic evidence of the as-built construction elements. Upon completion, an as-built assessment is carried out and submitted to an independent certifier, who has not been involved in the design of the building [10]. The building is then deemed a Certified Passivhaus.
In addition to certifying complete buildings, the Passivhaus Institut also awards certification to proprietary products and individual components such as windows, wall systems and MVHR units. These products are held on a database making it easier for designers to conduct quick comparisons between products and help with design. The use of certified products is not a necessity; however, penalties may be applied in cases where they are not used. In the case of windows, non-certified windows can be used if manufacturers supply data to EN 10077 so that the components worksheet in PHPP can be completed. Certifying products ensures quality and that materials will meet Passivhaus standards.
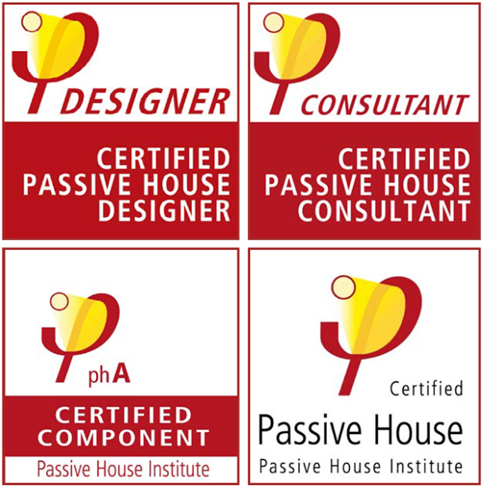
Figure 3: Passivhaus Certification
The importance of commissioning
Because a Passivhaus is exceptionally airtight, it relies heavily on the mechanical ventilation with heat recovery (MVHR) system to provide sufficient ventilation and prevent problems with indoor air quality and moisture. MVHR units are often installed in less accessible areas like the loft and usually operate quietly. Consequently, homeowners might not always know if the MVHR system is inactive, potentially leading to issues of condensation and mould.
It is crucial to conduct thorough commissioning of MVHR units. Additionally, a proper handover procedure post-commissioning is essential to educate homeowners about the system’s functioning and correct usage, ensuring effective ventilation and optimal performance.
Is certification necessary?
Certification is essentially a quality control process that ensures that the building will not only perform as designed but also will last. The PHPP software can be bought for £170+ VAT, and the cost per unit of certification for a Passivhaus is between £1,500 and £2,500[10]. Passivhaus Certifiers, designers and tradespersons will incur their own fees for training and registration.
Non-certified materials and systems may be used in Passivhaus designs provided one can provide the necessary parameters in PHPP for the calculation to be accurate.
It is possible to design and build using the fundamental principles of Passivhaus but not achieve the very strict targets required for certification. In situations where efforts have been made to achieve the Passivhaus standard, but they haven’t quite achieved it, it is possible to seek the Passivhaus Institut Low Energy Building standard (PHILEB). This is discussed further in Chapter 5 of the full report which can be found here.
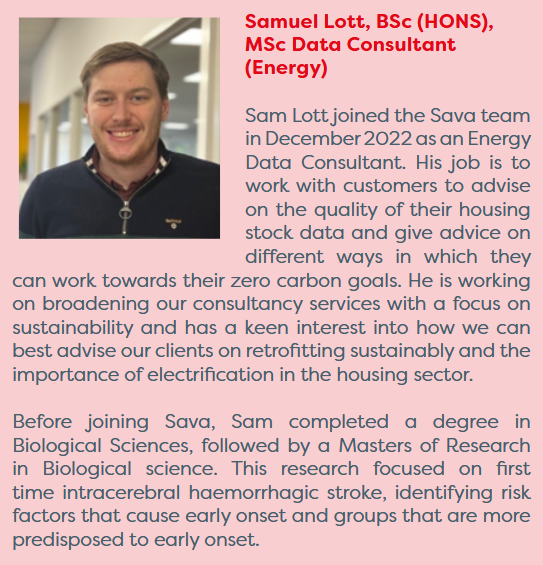
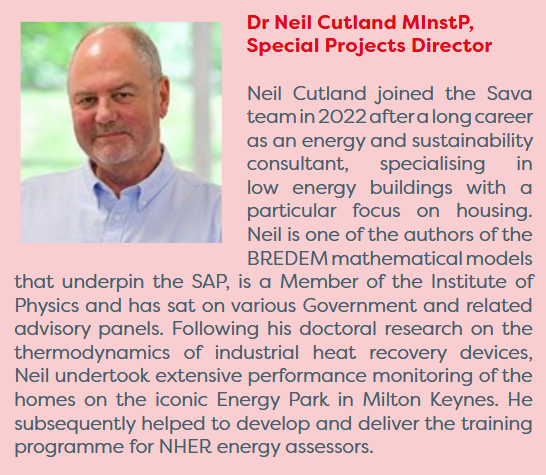
References
[1] Passive House Institute, “Criteria for Buildings Version 10c,” Passive House Institute, Darmstadt, 2023.
[2] Evidence for compliance with the non-renewable primary energy demand (PE) will still be accepted. In the Passivhaus Planning Package (PHPP) software the Passivhaus Institut have country-specific PE limit values based on primary energy factors. If no value exists for a country, then the default is a maximum of 120 kWh/m2yr.
[3] Heat loss is expressed as a measured or calculated U-value. U-values show how much heat in Watts is lost per square metre at a standard temperature difference of 1 degree Kelvin. To calculate the heat loss of an area such as a wall one therefore multiplies the U-value by the area and the temperature difference between inside and outside.
[4] For more detail see ‘Windows- making it clearer’ (NF77), 2017
[5] For further information see NHBC Standards chapter 6.2 – External timber framed walls.
[6] Passivhaus Trust, Members directory. Click here. [Accessed May 2024].
[7] More detail on the Home Energy Model can be found at: gov.uk/government/consultations/home-energy-model-replacement-for-the-standard-assessment-procedure-sap
[8] NHBC Foundation, “NF41: Low and zero carbon homes: understanding the performance challenge,” 2012.
[9] See passivehouse.com/03_certification/05_certified-tradesperson/05_certified-tradesperson.htm
[10] See passivehouse.com/03_certification/02_certification_buildings/03_certifiers/01_accredited/01_accredited.html
[11] Costs are correct as at November 2023