Grenfell Tower – What Have We Learned From Phase 1 of the Inquiry?.
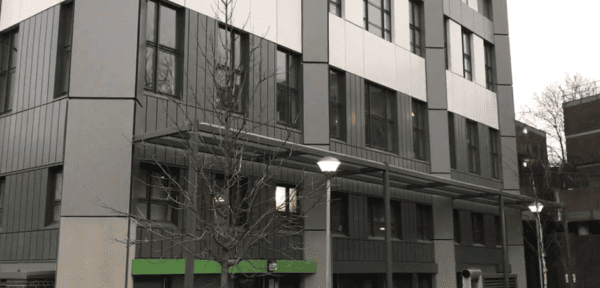
In October 2019 Phase 1 of the Grenfell Tower report was published by the Grenfell Tower Inquiry, convened under the chairmanship of the Rt Hon Sir Martin Moore-Bick. Phase 1 of the inquiry covered the cause of the fire, its subsequent development and the steps taken by the London Fire Brigade and the other emergency services in response to it.
In this article, we review the Phase 1 report to summarise what we currently know about the Grenfell Tower fire – how it started, how it spread and how it caused such a devastating loss of life.
This article focuses on the building, it’s construction and management, and the learnings the surveying and property management professions can take from the tragedy at this stage. It draws on the findings of the inquiry. It is not within the scope of this article to comment on the response of the London Fire Brigade or the ‘Stay Put’ policy whereby many residents waited to be rescued rather than escaping from the burning building.
Introduction
In the early hours of Wednesday, 14 June 2017, a fire broke out in a kitchen in one of the flats of Grenfell Tower. Kitchen fires are not uncommon and in terms of its origin and magnitude there was nothing exceptional about this one. However, as we all know, the fire escaped from the kitchen into the external envelope of the building.
The fire claimed the lives of 71 people who were present in the tower that night, including a child who was stillborn shortly after his mother had escaped and had been admitted to hospital. A total of 227 people in all (residents and visitors) escaped from the tower.
The Phase 1 report extends over 4 volumes, much of it very detailed information from the various expert witnesses and the London Fire Brigade. Chapter 32, however, is simply titled ‘Remembering those who died’ and respectfully remembers those people who lost their lives. For anyone involved in residential property it is worth reading because, while we tend to focus on the buildings themselves, we must remember that they are homes to real people.
Grenfell Tower – history and location
Grenfell Tower is a high-rise residential building in North Kensington, West London. It was built in 1974, though designed some years earlier in the late 1960s, and was owned by the Royal Borough of Kensington and Chelsea (RBKC) and managed by the Royal Borough of Kensington and Chelsea Tenant Management Organisation (the TMO).
Grenfell Tower is just over 67 metres tall and has 25 storeys consisting of a basement and ground and 23 upper floors.
The tower plan floor area is approximately 22 metres by 22 metres. It was constructed with a central reinforced concrete core, reinforced concrete floors and perimeter reinforced concrete columns at each corner of the building. The exterior surface of the perimeter columns were faced with pre-cast ribbed concrete panels (described as ‘biscuits’ in the Phase 1 report) secured via metal wires embedded in the concrete of the columns themselves.
At the time of construction, the exterior of the building comprised horizontal structural solid concrete spandrel panels (pre-assembled structural panels used as a separating wall) and sliding single glazed, aluminium-framed windows. The metal window frames were fixed directly to the concrete structure on three sides. There were also non-structural, white window infill panels. The material of these infill panels was unknown at the time of the Phase 1 report but may have contained an asbestos bearing cementitious material. The aluminium window frames were also directly connected to these infill panels.
At the top of the building is a pre-cast architectural “crown” which consists of tapered pilasters at the tops of the columns and a ring of perforated freestanding concrete beams.
Internally, the original window sills, jambs and heads were lined in timber. Above and below the windows were panels of ICI “Purlboard” (a layer of plasterboard with a layer of polyurethane foam bonded to the rear). The strip of Purlboard above the windows extended the full perimeter of the external wall in each flat.
Floors 4 to 23 were designed to accommodate residential flats, with six flats on each floor separated by reinforced concrete cross-walls. Floors ground, 1 and 3 were designed to provide more flexible community spaces, later a nursery, offices and a community health centre. Floor 2 was originally left open as a continuation of the walkway connecting adjacent low-level housing blocks.
Later minor refurbishments
• In 1985 the front doors of the flats were replaced. An application under the Building Regulations for the fitting of new self-closing, fire-resisting flat doors was made in 1985, but no further details are known about that work at this time.
• Between 2005 and 2006 both lifts were refurbished. The work appears to have included the “like for like” replacement of the two lift cars and the renovation of the lift motor room and associated equipment.
• Between 2011 and 2013 the entrance doors to the flats on floors 4 to 23 occupied by RBKC tenants were replaced. The purpose of the work was to replace 106 flat entrance doors with fire doors which complied with relevant fire safety standards. The remaining flats not listed for front door replacement were either tenanted or owner-occupied leasehold.
• Between 2016 and 2017 a new tenant gas supply was installed to serve the south-east corner flats because corrosion within one of the existing gas risers had led to a small leak in September 2016. The faulty riser was isolated and a new riser was installed. The new riser enters the building on the south-east side at the basement level and rises vertically through the central staircase between floors 2 and 23. At certain floors it was necessary to install a new lateral gas pipe which passes out through the stair wall, across the lobby and into the flat. The boxing-in of this pipework in the lobbies had not been completed at the time of the fire on 14 June 2017.
The main refurbishment
The most significant change to the building, and most referred to, was the refurbishment carried out between 2012 and 2016. During that period Grenfell Tower underwent substantial changes affecting both the outside and the inside of the building. As we all know, it incorporated the over-cladding of every storey of the existing building with a new insulation and rainscreen cladding system.
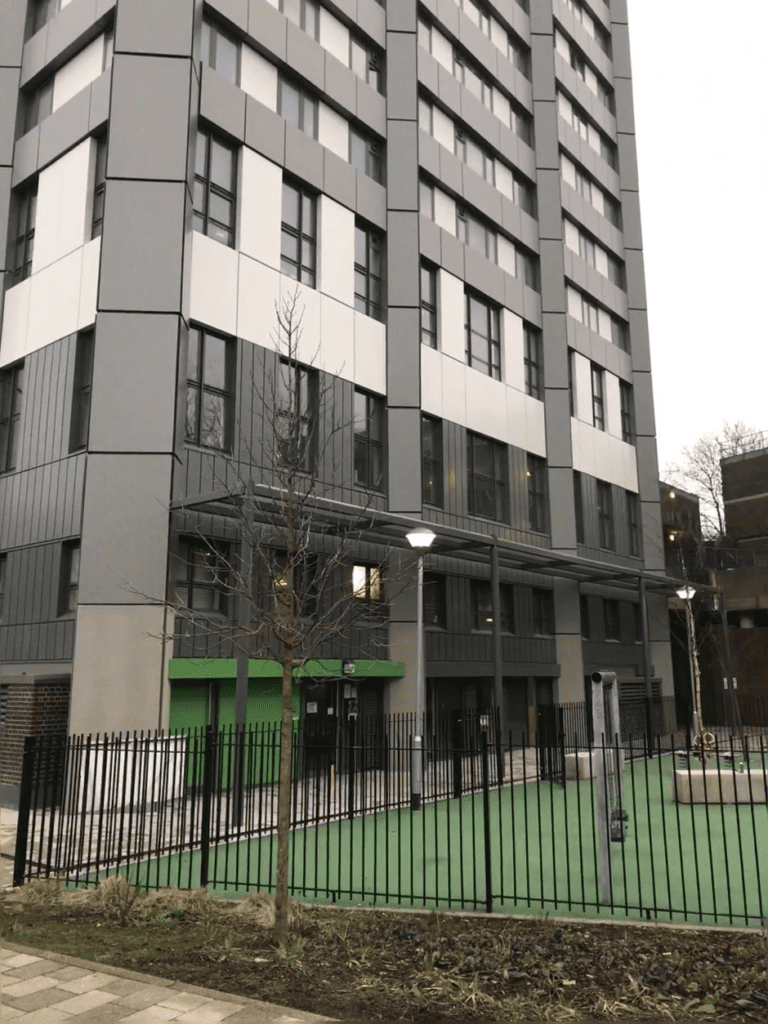
In addition to the over-cladding of the building, there was a full refurbishment internally of the very lowest floors from the ground floor to floor 3, including structural works. This included the creation of nine new flats on these lower floors and the relocation and refurbishment of the existing nursery and boxing club. Soft and hard landscaping works were also carried out in the area immediately surrounding the tower.
Building services works were carried out on every floor and within every flat. These internal building services works included the fitting of a new heating system to all areas, a new boosted cold-water distribution system and the refurbishment and extension of the existing environmental ventilation and smoke control system. There were also some alterations to the lifts and dry riser system.
The windows
New, smaller windows were installed on every floor. During the refurbishment the windows were moved outwards so that they no longer sat flush with the concrete but flush with the new cladding system. As the report notes, by repositioning the windows outside the line of the concrete structure and without providing a non-combustible barrier between the interior of the building and the cavity within the cladding system, the effective compartmentation of the building in the event of a fire was undermined.
The changes to the windows created gaps in what had, as a result, become part of the internal walls. For example, vertical gaps had previously existed between the outer corner of the concrete spandrels and the edges of the columns where the two abutted, but before the refurbishment they had formed part of the exterior wall. One result of repositioning the windows was to incorporate those gaps into the interior behind the new window frames. In some places the gaps were filled with an expanding polyurethane foam, in others they remained open.
Another example of this is that before the refurbishment there had been a sloping lip on the outside of the building beneath the windows. By repositioning the windows beyond the outside line of that lip, a horizontal gap below the windows was created.
The reduction in the size of the windows created a gap between the sides of the windows and the adjacent columns. The gap was covered with a black ethylene propylene diene monomer (EPDM) synthetic rubber weatherproofing membrane of 1mm thickness. EPDM is combustible and is thermally thin, which means it will burn quite rapidly. The EPDM was bonded to the window frame and the face of the concrete column, but in some places it was bonded between the two layers of spandrel insulation. Around the columns the EPDM membrane covered the cavity between the insulation and the rainscreen panels without any additional protection.
Internally new uPVC (unplasticised polyvinyl chloride) window sills, jambs and heads were installed around each of the windows on top of the existing timber window joinery, which was left in place. They had a uniform thickness of 9.5mm and a smooth white finish. The report noted that uPVC is a solid combustible polymer which begins to lose its stiffness at around 60°C and loses it entirely at about 90°C. It has an ignition temperature of between 318°C and 374°C. It chars when exposed to heat and generally displays limited surface spread of flame due to its high chlorine content. The uPVC window surrounds were glued partly to the pre-existing timber window sills, window heads and window jambs, and partly to 25mm insulation boards which were used to close off the opening into the cavity in the cladding caused by the repositioning of the windows. No mechanical fixings appear to have been used.
The 25mm insulation boards underneath the windows were a layer of PIR insulation, either Celotex TB4000 or Kingspan Thermapitch TP. These are both types of PIR insulation but were much thinner products than those used on the spandrels and the columns. (PIR [polyisocyanurate] boards are one of the most efficient insulation materials used in construction. This product is an improvement of previously used PUR boards [polyurethane], typically produced as a foam and used as rigid thermal insulation.) The original white window infill panels were retained behind new infill panels. The new panels were fitted flush with the new wall insulation, in effect creating a cavity between the original and the new panels.
The cladding
The cladding work involved the addition of a ventilated rainscreen insulation and cladding system attached to the original concrete façade, in effect creating a new external wall on the tower.
At floors 4 to 23 this comprised insulation materials, new windows and window infill panels (discussed above) and outer aluminium composite material (ACM) rainscreen panels. At floors 1 to 3 the outer wall was re-clad with glass-reinforced concrete castings on the columns and other types of rainscreen panels. The Phase 1 report does not deal with these floors as they were not involved in the fire.
The outer layer of the new external façade covered the existing concrete spandrel panels and the columns. This façade comprised ventilated rainscreen panels made of aluminium composite material (ACM) pre-fabricated into ‘cassettes’ which are hung on steel or aluminium supports fixed to the concrete structure.
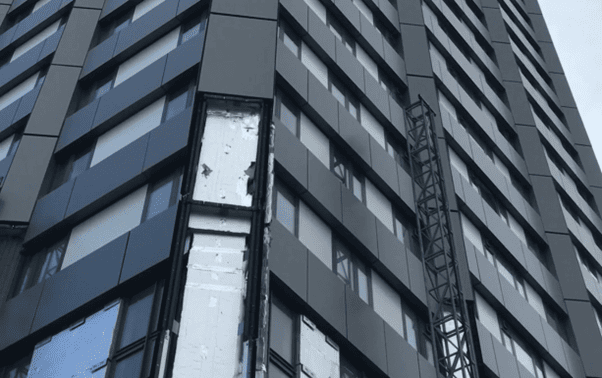
These systems are designed to protect a building from water, with the exterior surface providing the original protection layer. Some water will inevitably get through the outer layer and will seep through to the inner surface of the cladding where it will drain down via gravity. The cladding material is separated from the rest of the wall assembly by a small gap. It is called a ‘ventilated rainscreen system’ because it is designed to protect the building from the majority of direct rainfall but has gaps which are designed to permit the ventilation of the cavity behind the panels and ensure that water is collected and drained away.
The cladding panels consisted of a 3mm thick core of polyethylene bonded between two 0.5mm thick sheets of aluminium. The Phase 1 inquiry found that:
“Polyethylene is a combustible synthetic thermoplastic polymer which melts and drips on exposure to heat. It can flow whilst burning and generate burning droplets. It has a high calorific value compared with other common construction materials and will provide a fuel source for a growing and spreading fire. It melts at 130-135°C and ignites at around 377°C.”
The aluminium component melts at approximately 660°C and can warp and deform under the influence of heat.
Polyethylene is produced from ethylene, and although ethylene can be produced from renewable resources, it is mainly obtained from petroleum or natural gas.
On many of the panel edges used for the spandrels the polyethylene was exposed. The panels used on the columns were designed differently. One of the findings of the Phase 1 report was that the system of panels and fixings used for the Grenfell refurbishment appeared to have been uniquely designed for this specific project.
Behind the ACM panels used for both the spandrels and the columns there was a layer of insulation fixed directly to the building. On the spandrels this consisted of two 80mm layers of insulation board (Celotex RS5000 polyisocyanurate (PIR) polymer foam or in very limited quantities Kingspan K15 phenolic polymer foam). On the columns, the insulation consisted of one 100mm layer of Celotex RS5000 PIR with a small number of Kingspan K15 insulation boards. In some varying instances an additional piece of insulation board was located adjacent to the windows, alongside the columns. The insulation was fixed to both the spandrels and the columns by 180mm stakes screwed into the face of the existing concrete.
The ‘cavity’ between the insulation and the rain screen panels varied from 139mm on the columns to 156mm on the spandrels. In addition to the ‘designed’ cavities, the ribbed ‘biscuit’ finish on the columns resulted in additional ‘un-designed’ cavities.
The inquiry noted that while PIR is sometimes claimed to be fire retardant and is certainly more fire resistant that PUR, PIR and phenolic foam have a comparatively low time to ignition and can support rapid flame spread. They can also accelerate the spread of flame on adjacent materials by insulating the cavity and preventing energy from being lost from the system.
Cavity barriers were installed in the façade system in both the horizontal and vertical positions. These cavity barriers did not block the cavity completely. Rather they incorporated an intumescent strip designed to expand in the event of a fire. It was this act of expanding that would then intend to seal the gap between the barrier and the rear of the cladding.
In the horizontal position they were installed approximately 700mm below the level of the window sills and extended over the columns at that level. On both the columns and the spandrels they were mechanically fixed using metal support brackets which pierced the full depth of the barrier at 400mm centres.
Cavity barriers were not provided for all the columns and no cavity barriers were present at the nose of the columns or at the top of the building. In addition, they were not continuous because the cladding rails supporting the ACM panels broke through them at least every 1100mm and in many cases they were poorly fitted, with gaps between them instead of being tightly abutted.
Other changes
The other changes undertaken during this significant refurbishment included:
• A new heating system created for the whole of the tower. The existing boilers were retained to continue serving the walkways and a new central gas fired boiler to serve the tower was installed in the basement. Six new risers were put in to carry hot water to all floors and a new service cupboard was created in the lobbies on every level from level 4 upwards to accommodate the risers and return piping. In each lobby the pipes left the service cupboard and were concealed above a new plasterboard ceiling. They entered the individual flats via holes drilled through the concrete walls above the front door. Each existing residential flat was served by an individual heat interface unit (HIU), which was electrically operated and enabled the residents to control their heating and hot water. New pipework and radiators were installed in each flat.
A new boosted cold-water system to distribute cold water from a plant room at roof level. This also involved installing additional pipework in each of the lift lobbies which entered flats via holes drilled through the concrete walls.
• An environmental air control system in the common parts of the tower because the new services installed in the lobbies could cause them to become uncomfortably warm under normal conditions. The existing smoke control system was modified to become a combined environmental and smoke control system.
• At ground floor level a new dry riser inlet was installed to serve the existing dry rising main in the core of the building. This required new pipework on the lower floors of the tower in order to connect with the existing pipework at floors 4 and above with new landing valves and branches.
Occupancy and management
At the time of the fire most of the flats in the tower were occupied by RBKC’s social housing tenants. However, there were also 14 leaseholders of flats.
Although the tower was owned by RBKC, it was managed by the Royal Borough of Kensington and Chelsea Tenant Management Organisation (the TMO).
The TMO is a limited company appointed in 1996 by RBKC by way of a Management Agreement to carry out certain housing management functions.
How the fire started
The Phase 1 report concluded the fire was accidental and started by a kitchen appliance as a result of an electrical fault.
The fire started in flat 16 in the north-east corner of floor 4 of the tower. The occupant had been woken by his smoke alarm and saw that there were flames around his fridge/freezer.
This was not an exceptional occurrence. In 2018 Which? reported that faulty household appliances – primarily washing machines and tumble dryers – account for 60 house fires a week in the UK, with the number of fires staying roughly the same each year for five years.
While a household fire was not unusual, 10 minutes after the fire brigade arrived the fire broke out of the flat into the cladding on the outside of the tower and began to climb the building.
How did the fire break out of the flat and into the materials on the outside of the building?
The inquiry demonstrated that the smoke from the fire would have been around 110 – 220°C – not hot enough to ignite anything in the kitchen window or the cladding outside, but it would have been hot enough to impact on the uPVC replacement plastic window surrounds which start to melt and distort in temperatures as low as 70°C (when it becomes very viscose and behaves a bit like a gum). The fact that the uPVC window jambs were held in place by adhesive, with no mechanical fixings, made them all the more vulnerable to deformation in rising temperatures.
The uPVC was, however, covering a range of flammable materials – the EDPM synthetic rubber weatherproofing membrane and beyond that the insulation. The report notes that all the experts agreed that the uPVC near the fridge/freezer in the kitchen probably deformed at an early stage allowing flames access to the cladding system on the outside of the tower. Indeed, two firemen attended the fire inside the flat and put the fire on the appliance out. However, by that time the series of events were put in motion because they were aware of an orange flicker outside the kitchen window – this was the cladding burning.
Why did the fire spread so rapidly?
The fire spread in a straight line directly upwards. 18 minutes after it had escaped the kitchen window of flat 16 it reached the 23rd floor at the top of the tower. This rate of 4 metres a minute is noted in the report as being relatively slow when compared to other cladding fires around the world but must have been truly terrifying to anyone witnessing it.
Why did the fire spread so rapidly outside of the building?
All the expert witnesses called by the inquiry analysed the complex collection of materials used on the tower. The report concludes that although many factors played a part, the principal reason was the ACM rain screen panels and the polyethylene they contained. The report also says that it is more likely than not that the insulation behind these panels contributed to the speed of the fire. Sir Martin Moore-Bick writes: “I am satisfied that, although many different factors played a part, the principal reason why the flames spread so rapidly up the building was the presence of the ACM panels with polyethylene cores, which had high calorific value, melted and acted as a source of fuel for the growing fire. I also think it more likely than not that the presence of PIR and phenolic foam insulation boards behind the ACM panels (and perhaps the EPDM membrane and the Aluglaze window infill panels) contributed to the rate and extent of vertical flame spread”.
There were other issues covered in the discussions at the inquiry about the fire spread. One was whether the cladding design could have contributed to the spread, particularly because of long vertical channels along the columns.
For example, one expert witness, Professor Luke Bisby from the Edinburgh University School of Engineering, stated at the enquiry: “Having the fire confined in a corner, even if it is not a right-angled corner, does 2 things – it changes the way that fresh air is entrained into the fire which means, essentially, you are going to get less air entrained into the fire at its base because there is restricted access to the fire because of its confinement. That has the effect of elongating the flame as the flame searches for more air in order to continue burning, so you have flame elongation in a confined area which would exacerbate upward vertical fire spread”.
The report noted that it was very possible that vertical channels played a role in exacerbating the fire, but the Chairman, Sir Martin Moore-Bick, was unwilling to reach firm conclusions on this point.
Another issue discussed at the inquiry were the cavity barriers intended to stop the spread of fire on the outside of the building. Although many were found to be missing or incorrectly installed, the report concluded that this was not of great significance. Cavity barriers work because when exposed to heat they expand to block the cavity, in this case between the outer rain screen and the insulation on the side of the tower. Here the fire was actually inside the panels themselves so simply passed over the top of the cavity barriers.
Dr Barbara Lane, a fire engineer from Ove Arup, gave evidence to the inquiry and noted: “Cavity barriers cannot stop a fire in a cavity if the wall itself is burning. The very founding principle is that the wall is not burning, and the cavity barrier is stopping a flame in the cavity. The cavity barrier cannot stop the whole wall from burning in that position”.
(As an aside, the inquiry cannot possibly know that the cavity barriers would have functioned properly. I have seen videos of cavity barriers in test situations that eventually expanded to block the cavity, but only after the flame had spread over the barrier into the cavity above.)
Once the fire reached the top of the tower it started to move around and down, in effect wrapping around the building. The report concludes that this was a specific unusual feature of the way the fire spread at Grenfell. The report says that there were two main reasons for this:
• the rain screen panels – in particular the way the polyethylene core melted and dripped as it burnt resulting in more fires starting lower down the building which then travelled back up to the top.
• the architectural crown – a purely aesthetic feature at the top of the tower. The crown was made up of a series of U-shaped bent rain screen panels with an exposed edge of polyethylene at each corner.
As well as dripping molten material, the inquiry found that fire also spread downwards along the columns of the building, probably exacerbated by the long vertical cavities behind the rain screen on the columns, though it notes that more work is needed to see if any other routes of fire spread had a particular significance. At 2am, flames were travelling along the north and east sides of the tower. By 2.20am the fire had spread to the south side of the building and at 4.02am the two flame fronts met on the south-west corner meaning that the tower was completely encircled.
The report concludes that the outside of Grenfell Tower failed the functional requirement of the Building Regulations because the materials not only did not adequately resist the spread of fire over them, but instead promoted it.
This is a very significant issue for many affected by the fire ahead of Phase 2 of the inquiry. In arriving at this conclusion, the report effectively rejects submissions from 3 companies involved in the refurbishment of the tower who all stated that there was not enough evidence to reach this conclusion.
However, Sir Martin Moore-Bick reported that, despite this finding, he did not consider it appropriate to make recommendations at this point in the inquiry about whether materials of a certain fire safety rating should be banned from high-rise buildings or whether there should be changes to the testing and certification of materials.
“I intend in Phase 2 of the Inquiry to examine (among other things) the extent to which the regime for testing materials intended for use in external walls (including thermoplastic polymer materials such as polyethylene) and the regulations governing their use were, and are, adequate to identify and control the potential dangers from downward and horizontal as well as vertical flame spread. I shall also examine what was and should have been known, both by those in the construction industry and by those in central government responsible for setting fire safety standards, about the particular dangers posed by thermoplastic polymers.”
The report does recommend that the owners and managers of high-rise buildings should be required by law to tell the local fire and rescue services about the materials put on the outside walls. However, on the issue of whether panels containing polyethylene should be removed from other buildings around the country Sir Martin said it was unnecessary for him to make this into a recommendation because this has already been accepted.
What happened inside the building?
The fire on the outside of the building was dramatic, but was it inevitable that it would enter the flats from the outside? We know from the inquiry that the fire did indeed enter many flats and smoke spread rapidly through the interior of the building.
We know that some residents had left their windows open because it was a hot summer night but, even if that was not the case, Sir Martin accepted the argument that even if windows were closed, the glass in the windows could not withstand the high heat from the fire in the cladding. In addition, extractor fan units in the kitchen windows buckled and failed when subjected to the heat providing a point of entry for the fire even if the glass had not failed. As a result, the inquiry concluded that effective compartmentation was lost at an early stage.
The first flats to be affected by the fire when it spread in a straight line up the building were those ending in the number 6 – all residents of those flats quickly left.
In addition, a number of other key fire protection measures inside the tower failed. Although some fire doors held back the smoke, the inquiry concluded that others did not. The inquiry identified that on 5 floors the doors to these number 6 flats (those first affected by the fire rising on the outside of the building) did not close behind people because their self-closing mechanisms did not work. Therefore, smoke spread from these flats into the communal lobbies.
Doors on 2 additional floors were also left open for less clear reasons.
The report took so many witness accounts that it was able to track the movement of the fire around the building. Approximately 26 minutes after the first 999 call the communal lobbies on several floors had started to fill with smoke. The situation varied slightly from floor to floor, but less than half an hour after the first 999 call the smoke on the 10th floor, where the door to flat 76 was open, was so thick it trapped 3 people. Sadly, they did not survive. By 2am, just over an hour after the fire was reported, a significant number had become smoke logged.
It seems that the lobbies filled more quickly than the stairs. The report identified that until around 1.50am there was less smoke in the stairs and by that time 168 people had been able to escape the fire. However, after that time the stairs also started to fill with smoke, particularly at the lower levels. Though it was not consistent in the stairs, smoke was thick and the heat considerable. By 2.20am the inquiry found that the smoke in the stairs did pose a risk to life, although the stairs were not completely impenetrable to all even after that time since people did successfully continue to use the stairs until 8.00am. That said, the report did also identify that between floors 13 and 16 the heat was so intense that light fittings were later found to have melted.
The inquiry concluded that some of the fire doors failed. Whether the fire doors at Grenfell complied with Building Regulations will be a question for Phase 2. As this is such an important issue the report made the following recommendation:
“That the owner and manager of every residential building containing separate dwellings carry out an urgent inspection of fire doors to make sure they comply with current standards and that the law changes to compel all owners and managers of these buildings, whether or not they are high-rise, to carry out checks on fire door self-closing mechanisms every 3 months.”
Phase 1 recommendations
Recommendations from Phase 1 of the inquiry are covered in chapter 33 of the report. Those reported below are not all the recommendations or observations, rather they are a selection of those pertinent to housing managers and residential practitioners.
Regarding compartmentation, the report notes:
“Effective compartmentation is likely to remain at the heart of fire safety strategy and will probably continue to provide a safe basis for responding to the vast majority of fires in high-rise buildings. However, in the case of some high-rise buildings it will be necessary for building owners and fire and rescue services to provide a greater range of responses, including full or partial evacuation. Appropriate steps must therefore be taken to enable alternative evacuation strategies to be implemented effectively.”
Turning to the cladding, the report noted that surveys undertaken since the Grenfell tragedy have identified that external wall materials similar to those used on Grenfell Tower have been used on over 400 other high-rise residential buildings around the country. The report does not recommend removal since “… it is accepted that that must be done.”. However, in the meantime it does make the following observation:
“From the evidence put before me in Phase 1, two very important matters have come to light: first, that in its origin the fire at Grenfell Tower was no more than a typical kitchen fire; second, that the fire was able to spread into the cladding as a result of the proximity of combustible materials to the kitchen windows. It is not possible to say whether the same or a similar combination of design and materials is to be found on any other buildings, but it would be sensible for those responsible for high-rise buildings with similar cladding systems, if they have not already done so, to check whether the same or a similar combination exists.”
Additional recommendations relating to testing of materials etc. were considered not appropriate at this stage.
Regarding the fire services, the formal recommendation pertinent to building owners and managers is as follows:
“…that the owner and manager of every high-rise residential building be required by law to provide their local fire and rescue service with information about the design of its external walls together with details of the materials of which they are constructed and to inform the fire and rescue service of any material changes made to them.”
“…to provide their local fire and rescue services with up-to-date plans in both paper and electronic form of every floor of the building identifying the location of key fire safety systems.”
“…to ensure that the building contains a premises information box, the contents of which must include a copy of the up-to-date floor plans and information about the nature of any lift intended for use by the fire and rescue services.”
Regarding lifts in buildings, the recommendations are as follows:
“…that the owner and manager of every high-rise residential building be required by law to carry out regular inspections of any lifts that are designed to be used by firefighters in an emergency and to report the results of such inspections to their local fire and rescue service at monthly intervals.”
“…that the owner and manager of every high-rise residential building be required by law to carry out regular tests of the mechanism which allows firefighters to take control of the lifts and to inform their local fire and rescue service at monthly intervals that they have done so.”
Regarding evacuation, the recommendations are as follows:
“…that the owner and manager of every high-rise residential building be required by law to draw up and keep under regular review evacuation plans, copies of which are to be provided in electronic and paper form to their local fire and rescue service and placed in an information box on the premises.”
“…that all high-rise residential buildings (both those already in existence and those built in the future) be equipped with facilities for use by the fire and rescue services enabling them to send an evacuation signal to the whole or a selected part of the building by means of sounders or similar devices.”
“…that the owner and manager of every high-rise residential building be required by law to prepare personal emergency evacuation plans (PEEPs) for all residents whose ability to self-evacuate may be compromised (such as persons with reduced mobility or cognition).”
“…that the owner and manager of every high-rise residential building be required by law to include up-to-date information about persons with reduced mobility and their associated PEEPs in the premises information box.”
Relating to internal signage, the following recommendations were made:
“…that in all high-rise buildings floor numbers be clearly marked on each landing within the stairways and in a prominent place in all lobbies in such a way as to be visible both in normal conditions and in low lighting or smoky conditions.”
“…that the owner and manager of every residential building containing separate dwellings (whether or not it is a high-rise building) be required by law to provide fire safety instructions (including instructions for evacuation) in a form that the occupants of the building can reasonably be expected to understand, taking into account the nature of the building and their knowledge of the occupants.”
For fire doors the recommendations are as follows:
“…that the owner and manager of every residential building containing separate dwellings (whether or not they are high-rise buildings) carry out an urgent inspection of all fire doors to ensure that they comply with applicable legislative standards.”
“…that the owner and manager of every residential building containing separate dwellings (whether or not they are high-rise buildings) be required by law to carry out checks at not less than three-monthly intervals to ensure that all fire doors are fitted with effective self-closing devices in working order.”
“…that all those who have responsibility in whatever capacity for the condition of the entrance doors to individual flats in high-rise residential buildings, whose external walls incorporate unsafe cladding, be required by law to ensure that such doors comply with current standards.”
And what of Phase 2?
Phase 2 of the report will consider further the building itself and, in particular, the decisions which led to the installation of a highly combustible cladding system on a high-rise residential building and the wider background against which those decisions were taken.
In addition, Phase 2 will consider whether the current regime for testing materials used in high rise construction is as rigorous as it should be and if it is enforced properly. Sir Martin writes:
“These concerns extend to the adequacy of the regulations themselves, the quality of the official statutory and non-statutory guidance currently available, the effectiveness of the tests currently in use, arrangements for certifying the compliance of materials with combustibility criteria and the manner in which materials are marketed. They are questions that will lie at the heart of the Inquiry’s investigations in Phase 2.”
It will also consider further the detailing around the windows.
Regarding the fire doors, Phase 2 will look at how so many of them failed to be working properly (how they failed to close after residents had left) and how they were allowed to remain in this condition.
Phase 2 will not look at the staircase or the electricity but will consider the gas supply to the building, and in particular if it was compliant with the regulations in force at the time.
Conclusions
At this stage it is difficult to know quite how things will move forward. Following close on the heels of the Hackett Report (Published in May 2018) where Dame Judith Hackett concluded that “the regulatory system covering high-rise and complex buildings was not fit for purpose” and needed a “radical rethink of the whole system and how it works… not just a question of the specification of cladding systems, but of an industry that has not reflected and learned for itself, nor looked to other sectors”, it is difficult to see how there can be any regulatory changes until Phase 2 of the Grenfell report is published and the full picture is known.
That said, there have been some changes since the Grenfell tragedy. Notably, the Government acted quickly to introduce policy banning combustible material on some newly built property with effect from 21 Dec 2018 and has directed that in certain circumstances aluminium composite material (ACM) external wall systems are to be removed from residential tall buildings. They have also introduced comprehensive guidance via 22 separate guidance notes, most notable for residential surveyors being MHCLG Advice Note 14 for circumstances where there are other potentially combustible materials on existing tall buildings. These include but are not limited to: metal composite materials (MCM) faced with other metals such as zinc, copper and stainless steel; high pressure laminates (HPL); and rendered insulation systems.
Surveyors involved with the valuation, ownership and management of buildings containing multiple individual flats or maisonettes must maintain up-to-date knowledge of government advice, but until the outcomes of Grenfell are formally recognised and acted upon it is possible that Sir Martin Moore-Bick’s recommendations reported above will be taken as ‘best practice’. Consequently, residential property professionals should, at the very least, be familiar with them.