Underfloor Spray Foam Insulation.
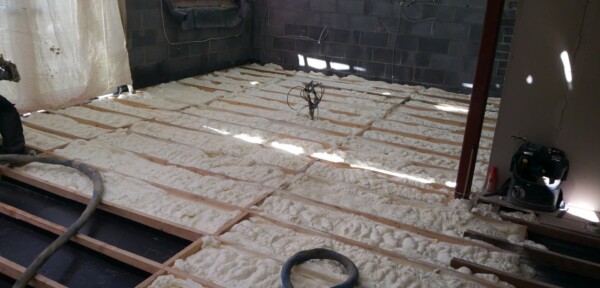
Waltham Forest Borough Council has recently undertaken a comprehensive retrofit of energy efficiency measures on a property at 47 Greenleaf Road, a typical Victorian end terrace property in Walthamstow, east London.
Built in 1902, the property was typical of its age with poor energy performance, an EPC energy rating of E, and an annual heat demand of 17,219kWh.
This article looks briefly at the measures installed, and in particular, at the underfloor insulation solution employed at the property.
Background
In 2019, the London Borough of Waltham Forest published a report indicating that 51% of its carbon emissions came from the residential homes within the borough. The borough is representative of many urban areas with 70% of the housing dating from before the second world war. In Waltham Forest’s case, this amounts to 107,216 homes.
Waltham Forest also wanted to address the issue of fuel poverty. At the time of the report, 14.6% of households in the borough were in fuel poverty (in 2019, across England as a whole it was 13.4% or 3.18 million households in total).
Fuel poverty in England is measured using the Low-Income Low Energy Efficiency (LILEE) indicator. Under this indicator, a household is considered to be fuel poor if:
- they are living in a property with a fuel poverty energy efficiency rating of band D or below
and - when they spend the required amount to heat their home, they are left with a residual income below the official poverty line
There are 3 important elements in determining whether a household is fuel poor:
- household income
- household energy requirements
- fuel prices
Source: UK Government
Consequently, Waltham Forest challenged contractor Aston Group to reduce the annual heat demand of 47 Greenleaf Road from 17,219kWh to 7,995kWh per year, and increase the EPC from an E to A.
Fabric First
Approximately 25% of the heat generated in the home will be lost through the roof, 35% through the walls and draughty windows and doors, and about 10% through the floor. Consequently, Aston started with the building heat loss envelope.
Walls – External wall insulation (EWI) was installed to the side and rear elevations of the property, using 90mm Rockwool insulation slabs (non-combustible) with a top-coat of render. EWI was not feasible on the street elevation in order to avoid loss of character to the property, therefore, internal wall insulation (IWI) was installed to this façade using a Celotex 57.5mm insulated plasterboard. To avoid cold bridging, the EWI and IWI were overlapped by one metre at the corners.
Roof – The roof was upgraded to 300mm of mineral wool insulation (between and above joists).
Underfloor – Floor insulation was installed to the main suspended floor via a ‘Q-Bot’ insulation system.
Underfloor insulation
The loft space is an established insulation method, and EWI and IWI are becoming more commonplace. The property, typical of its type and age, had wooden suspended timber flooring and the method chosen for the underfloor insulation is a new technology called the Q-Bot insulation system.
In fact, Q-Bot technology is not so new as it is a spray foam insulation system. What makes it a new, and potentially exciting innovation is that it uses small robots to access the floor void without disrupting the whole floor, thereby causing the minimum amount of occupier disruption.
And this is where the alarm bells will start ringing for many surveyors – spray foam insulation on timber.
What is not clear from the literature available is the condition of the floor prior to the work being undertaken, but as part of the installation process, AirEx smart air bricks were also installed into the walls to regulate airflow.
The AirEx ‘brick’ is a smart ventilation system that replaces existing air bricks at a sub-floor level. AirEx bricks have in-built sensors to measure the environmental conditions (such as temperature and relative humidity) and use smart software to automatically regulate airflow enabling the bricks to open to reduce humidity and prevent damp and associated problems such as mould, but to close to reduce heat loss and improve thermal comfort. The bricks are battery powered, the batteries need to be changed approximately every two years, and they link to a central ‘hub’ via the wifi system. More information can be found at https://www.airex.tech/
The Q-Bot system can apply insulation to a typical house in 1-2 days resulting in a SAP improvement of 2 to 12 points (which Q-Bot says has been verified by the Energy Saving Trust). The company claims the installation reduces the risk of damp and mould because the layer of foam creates a hydrophobic barrier between the floor and void, and by increasing insulation raises the temperature of the floor, thereby reducing the risk of condensation.
Several Local Authorities and Housing Associations have worked with Q-Bot to install underfloor insulation in a range of case study properties to demonstrate the improvement in energy and environmental impact and enhancement of residents’ comfort. These case studies have demonstrated improved U-values and high levels of occupants’ satisfaction. However, it is not clear if any long-term monitoring of the properties is being undertaken to establish any other side effects from the technology.
Lenders and spray foam insulation
We understand that a recent meeting involving several lenders and leading valuation firms reacted to the news of underfloor spray foam insulation with a “collected horror”. However, we approached two lenders for more detailed comments and the response was not completely negative.
While the general consensus is that any concerns relating to ventilation and dampness in roof spaces were magnified for under floor areas, one leading high street lender did tell us that for roofs, they would consider open cell foam when installed by an approved installer with all of the certificates and guarantees, but not where it has been used to rectify pre-existing roof defects. To the best of our knowledge, they have not yet had to address underfloor spray foam.
Nationwide also gave us the following statement:
“Regarding Spray Foam in roofs – we have reviewed our position and will accept this form of ‘insulation’ but only after the homeowner can demonstrate that the installation has been completed entirely in accordance with the manufacturer’s specifications (and that includes pre-instal survey, inclusion of barriers etc.). Otherwise, we would need a report form a Building Surveyor and will be guided by their recommendations. We would also require confirmation that the project was being implemented/designed to address energy efficiency as opposed to a short term roof repair/deficiency.
We are aware of robot technology for Spray Foam in under-floor voids – and we are currently looking at our guidance in this respect. The initial thinking is that our position will be similar to roof spaces i.e. ‘if’ it can be demonstrated that the ‘insulation’ has been installed correctly and in ‘full’ compliance with recommendations (inc pre-instal surveys etc), then we would accept it.
For example, the BBA specification states that services/wiring needs to be re-routed/protected and not covered with the foam, but we have seen photographic evidence that suggests this is not always achieved and indeed would be difficult to achieve without expensive and disruptive work, thereby, negating the benefit of the robot method of installation.”
The retrofit home
The Waltham Forest house refit is claiming an 82% improvement in energy use, 81% improvement in carbon emissions, and 64% improvement in running costs (calculated before the recent energy cost crisis).
Service upgrades
Mechanical ventilation – to reduce heat loss and improve internal indoor air quality, a mechanical ventilation system with heat recovery was installed
Heating system replacement – the existing gas boiler was replaced with an air source heat pump, associated hot water cylinder and new radiators
Photovoltaic array – A 3.9 kWp solar photovoltaic array has been installed with associated battery storage
A waste water heat recovery system (WWHRS) was fitted beneath the bath to recover a percentage of the heat lost down the drain.
While this article has only touched on the insulation and in particular the underfloor insulation, it will be interesting to see how this house performs over time and whether challenges such as the way the occupants live in and “manage” the house, together with the efficacy of the new technologies and any unforeseen consequences (particularly the underfloor insulation and the AirEx bricks), impact on the fabric of the property.
However, the energy efficiency and property running costs are no longer side shows; they have become mainstream issues. As so much of the UK housing stock is pre-war, innovative technologies are going to be essential if we are to address the issues of climate change and energy costs. Watch this space.
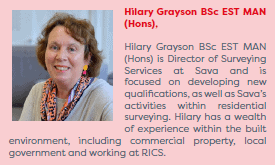