Unsafe Gas Installations.
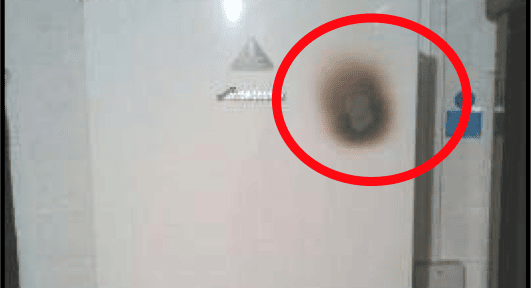
Negotiating your way through a property whilst giving due consideration to any gas installation can be a tough challenge, and while a Gas Safe registered engineer is sufficiently qualified to inspect gas installations, it is worth residential practitioners ensuring a high level of appreciation and understanding of what a safe installation should look like, and more importantly what an unsafe installation looks like.
Where to start?
Aside from the gas safety installation and use regulations, which underpin much of the legislative requirements around gas installation, there is also a normative reference document called ‘Gas industry unsafe situations procedure’[1], which is specifically used by gas engineers to interpret and decide on required action based on the severity of any unsafe situation. It’s a useful document for anyone working in the built environment.
The following insight is very much a brief, snapshot interpretation of the procedures, and should in no way be given precedence over the legislative document.
Legislation
The ’Gas safety installation and use’ regulations encompass all areas of gas safety in a domestic dwelling (they do not cover commercial property, unless there are areas of a commercial property which are legitimately used as sleeping accommodation).
As you might imagine, it’s a wide-ranging document but for the purposes of this article, I place emphasis on Regulation 29 which states:
“(9) Where a person performs work on a gas appliance he shall immediately thereafter examine –
(a) the effectiveness of any flue;
(b) the supply of combustion air;
(c) its operating pressure of heat input or, where necessary, both;
(d) its operation so as to ensure its safe functioning”
This is important because, for the most part, where any installation has suitable flue configuration to exhaust products of combustion and the appliance installed (if required) has an adequate supply of air to fuel the combustion process and is burning the right amount of fuel with no leakage of gas into the atmosphere, it’s likely an installation that will not cause harm to any homeowner and will work efficiently (subject to a regular servicing regime).
From a surveying perspective, this may be difficult to establish without a full commissioning procedure taking place, which you may not be qualified to undertake or may not be within the remit of the service or survey being carried out. However, there are several visual inspection activities which could help inform a professional opinion.
Appendix 5 of the ‘Gas industry unsafe situations procedure’ defines some specific visual inspections which can assist in identifying an unsafe installation operation.
1. Signs of distress – Are there any signs of distress on the gas appliance/surrounding area (e.g. discolouration/heat damage etc.) See figure 1 below.
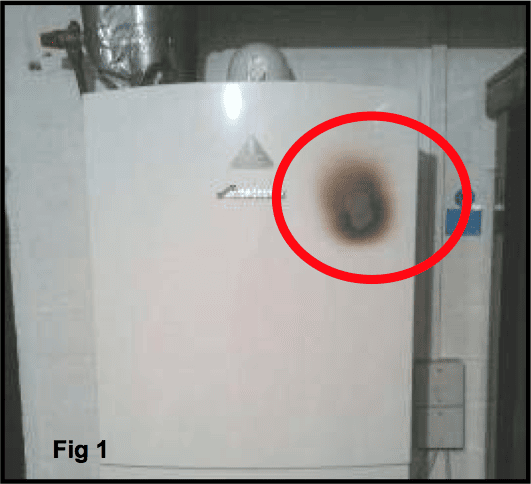
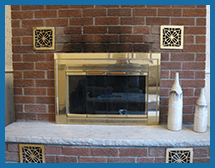
Figure 1 and 2
These are relatively extreme examples. You will note the boiler shows clear discolouration without needing to remove the casing. This is a clear sign of heat damage from inside the appliance which would be considered as immediately dangerous and further investigation would be urgently required.
The gas fire is showing signs of spillage of the products of incomplete combustion, suggesting that there is either inadequate ventilation in the room to assist in drawing fumes up and out of the flue/chimney, or perhaps the flue/chimney has a blockage which is preventing the flow of products out of the property. Again, without further inspection or evidence that a repair has been made and the discolouration was pre-existing, this would have to be deemed immediately dangerous.
2. Stable/secure – Is the appliance installation stable and secure? (e.g. will the appliance remain fixed and has it been installed in a manner that will not result in it becoming unstable?) See figures 3 and 4 for some examples.
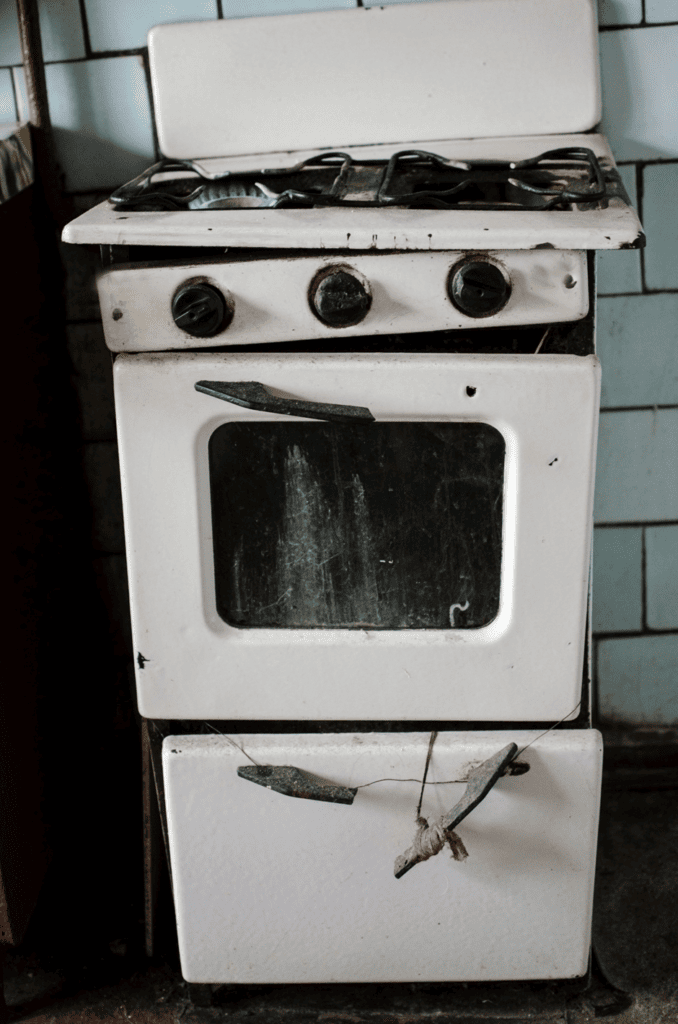
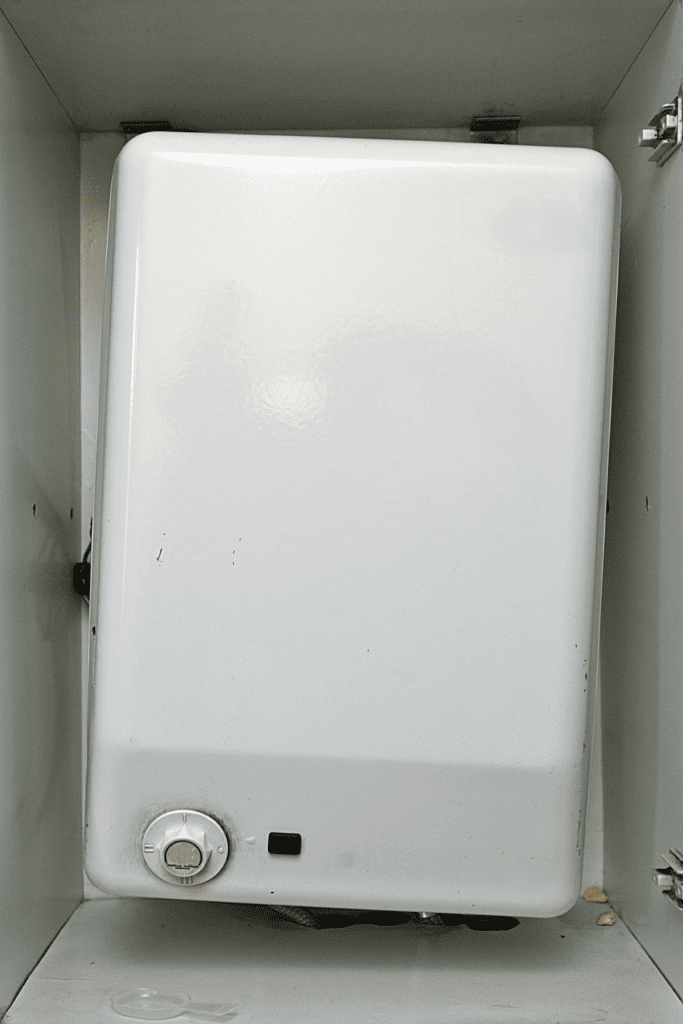
Figure 3 and 4
3. Location – Is the gas appliance installed in a suitable room and/or space as per regulations? For instance, an open flued appliance installed in a bathroom or shower room, or a flueless appliance installed in an undersized room would not conform to the regulations.
The majority of flueless appliances in homes are gas cookers, although you may also come across flueless gas fires and single point water heaters. Considering a gas cooker installed in a kitchen as an example, it would need to conform to the room and ventilation requirements in figure 5 below:
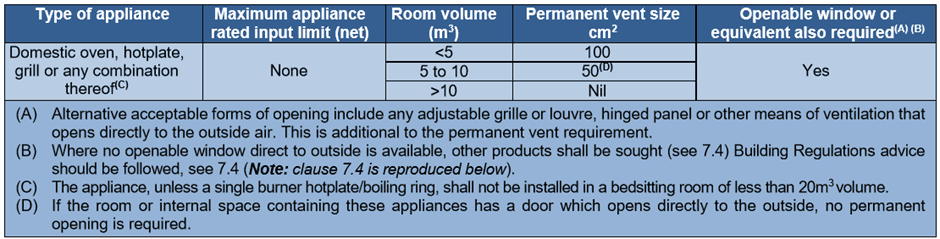
Figure 5
4. Flueing – If the gas appliance is flued (either open flued or room sealed) is there provision for adequate methods for the removal of the products of combustion to the atmosphere?
Figure 6 below shows the ventilation requirements for flued gas appliances. A gas engineer would use this guide to accurately determine if the existing size of vent installed is adequate to provide combustion air for the appliance (this does not apply to decorative gas fires).
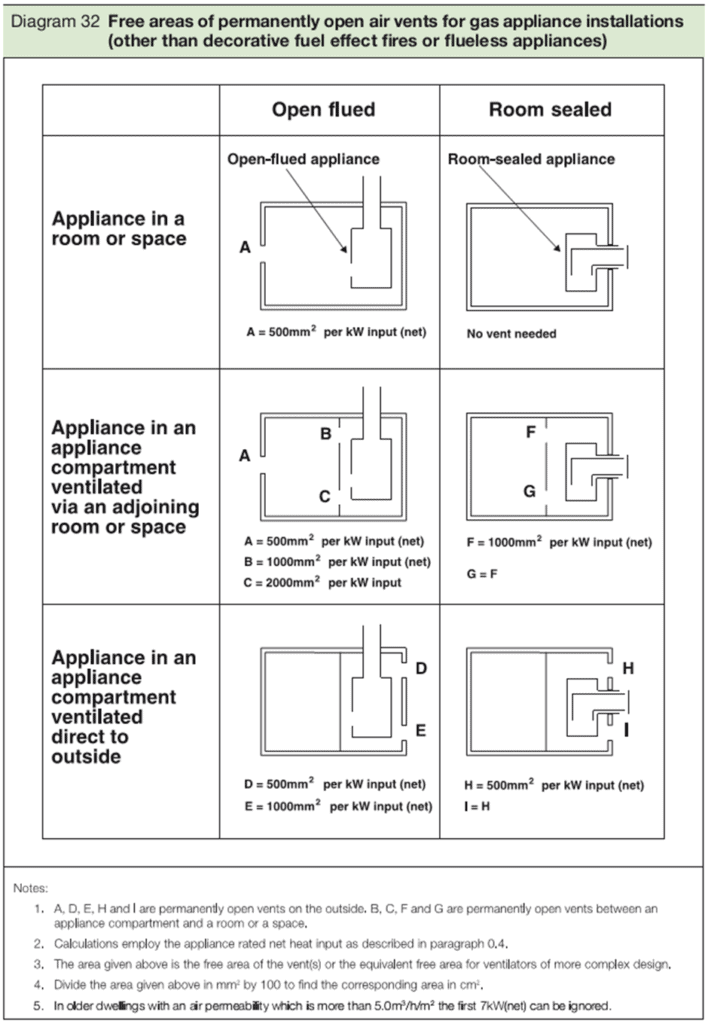
Figure 6
You will note that it is calculated using the net KW input of the appliance in question. This information may be visible on the appliance without removing the casing, exampled in figure 7 below, or it can be taken from the installation manual (figure 8).
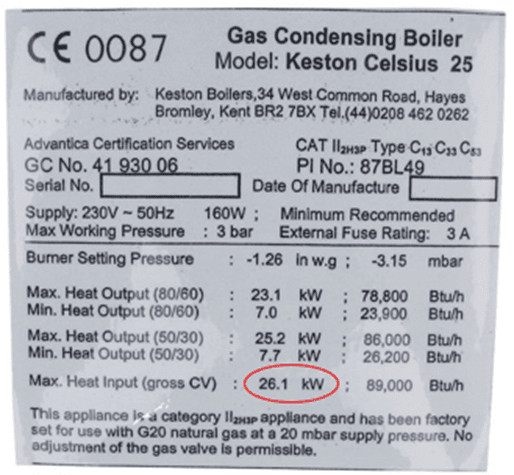
Figure 7

Figure 8
Using the information highlighted, you can determine the ventilation requirement for a specific appliance. Where the boiler badge (figure 7) relates to the appliance installed and is situated in a room with ventilation directly outside, using the table in figure 6 again, we can determine that the appliance requires 500mm2 (5 cm2) of ventilation per KW. As the ‘Max Heat Input’ is 33.76 the calculation will be 5 x 33.76 = 168 cm2.
5. Picture – If the flame picture is visible on the boiler, is it correct for the appliance type?
Many modern boilers have no way of viewing the flame picture whilst burning, however, many more traditional boilers do. If you can see the appliance and it is in operation, can you see a crisp blue flame? This demonstrates the gas and air mixture is sufficient to adequately oxygenate the flame. When the flame is starved of oxygen, the flame picture can start to turn much more floppy and yellow. For a radiant gas fire, cooker or boiler, a yellow, floppy flame indicates a combustion issue.
An exception to the rule applies to decorative fuel effect gas fires. As they are designed to provide a realistic ‘coal like’ flame, they tend to have a much higher gas rate and so effectively burn much ‘richer’ to provide a floppier flame.
Conclusion
Clearly, wherever there is any level of doubt or uncertainty, then recommending the need for a competent gas engineer will be essential, however, like all aspects of effective surveying, it is building up a story of all these incremental elements that starts to better inform you as to what the issue might be and what course of action might be required.
However, I believe it is also essential that surveyors and other property professionals have a basic understanding of how services work and can recognise the indicators that suggest they might be dangerous. While it is unlikely that installations with the failings illustrated in this article would have a gas safe certificate, it is not impossible. Things can change – and the certificate is only valid on the date of the inspection. In such a situation, an occupant might be at risk of injury or worse, and as property experts I believe we owe owners and occupants alike a duty of care to be able to point out things that need urgent attention.
[1] https://www.gassaferegister.co.uk/media/2622/igem-g-11-gas-industry-unsafe-situations-procedure-april-2018-amendments.pdf