Indirect Cold-Water Systems – Health and Safety Implications.
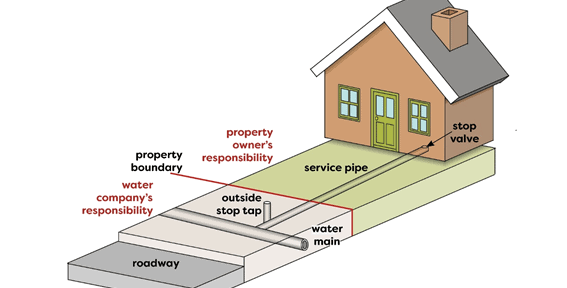
The new RICS Home Survey Standard refers to risks to occupants, specifically in paragraph 4.5 as follows:
“…matters that an RICS member or regulated firm is aware of that present a safety risk to occupants must be described in the report. Member should consider concisely listing the risks in a separate section with appropriate cross-referencing to where they appear in the report.”
Appendix E of the report provides a list of typical safety hazards in a dwelling. While lead pipes and Legionnaire’s disease are specifically mentioned in Appendix E, there is no other mention of potential hazards associated with cold water systems (though it is specifically stated in Appendix E that the published list is not intended to be exhaustive).
This article looks at indirect cold-water systems and the potential for harm that they may cause.
What is an indirect cold-water system?
Every property should have what is known as a ‘wholesome water supply’ – this is water fit for drinking, cooking food, or washing without any potential danger to human health by meeting the requirements of regulations made under section 67 of the Water Act 1991. Usually, water is supplied to the property directly from the water service pipe underground. The pipe will run from the road and enter under the house or through the garden or accessway, and it will enter the house via the household stopcock valve which is usually located underneath the kitchen sink. (Note: this is not always the case and if the water supply cannot be located in the kitchen further investigation may be required.)
An indirect cold-water system was the most common type of water system in the UK; although, new systems are now usually direct water systems. At the entry point, the water supply divides, with drinking water supplied to the kitchen sink, and the rest of the water is moved to a cold-water storage tank (usually located in the loft), which supplies the water for the rest of the house.
A direct water system does not have a storage cistern. Instead, the water is supplied directly to all taps and toilets directly from the mains.
An indirect system is more common in older properties where only the kitchen tap will be fed directly from the mains. Other taps will receive water from the cold-water storage tank located in the roof space. Very rarely are all the cold-water taps fed from the tank and there is no cold-water supplied direct from the mains.
If you are unsure of where the water supply is coming from you can test a water appliance by placing your thumb under the tap and testing the pressure. If you can stop the water flow with your thumb it is most likely supplied from the cold-water tank in the loft. A very important point to note is that with this water being indirect, it is not wholesome and therefore should not be used as drinking water, though many will use this water to wash or brush their teeth. The condition of the tank is therefore of the utmost importance.
Note: although a direct water system does not have a cold-water storage tank to supply the cold water taps in the property, some direct water systems will have a tank to supply the hot water storage vessel.
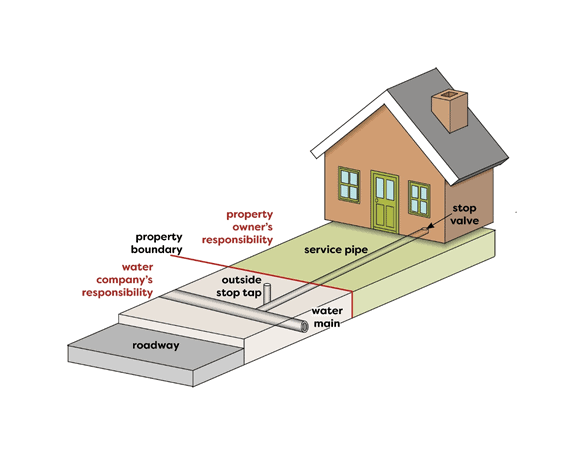
Figure 1: Water pipe running from street level under the property, note where the property owner assumes responsibility
Health and safety
There are a range of issues to consider concerning the safety of occupants and cold-water storage tanks:
Stability of the tank itself – water is heavy, and a large amount of water storage is usually needed. The tank must be adequately supported.
Protection against frost – there is a greater risk of frost damage to pipework and cisterns in the roof space.
Damaged ball valve – the ball valves allow water to enter the tanks through the inlet pipe to refill the tank when water is drawn off. When the water reaches a certain level the ball valve will close the inlet pipe. When it fails, water will continue to enter the tank and will lead to the tank overflowing. This could be slight and simply a drip from the overflow pipe which should be noticed by the property owner or indeed surveyor and resolved or the fault can be more serious resulting in a sizable leak and significant damage.
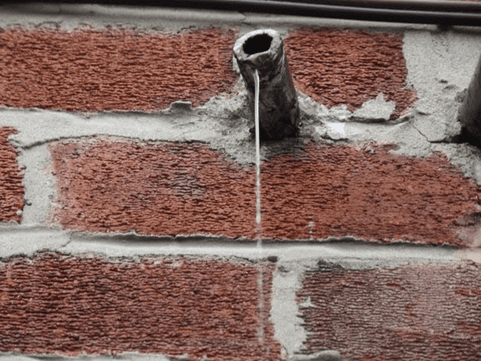
Figure 2: Dripping overflow pipe
The internal condition of the tank – this will have a direct impact on the quality of stored water and conditions may arise that encourage the proliferation of pathogenic bacteria, including Legionella. Tiny, suspended solids and dissolved solids in the mains water settle and collect at the bottom of the tank as sediments which serve as nutrients that encourage bacteria growth.
The ambient temperature around the tank – this again can encourage the proliferation of bacteria.
The ‘hardness’ of the water supply – hard water can contain relatively high concentrations of calcium and magnesium that contribute to the formation of scale and provide nutrients for bacteria.
The size of the pipe supplying the tank – the combination of an oversized mains inlet pipe and a relatively small outlet can also lead to water stagnation.
Coverings missing or damaged – can lead to contamination from dead animals and birds or decaying vegetation (leaves etc.) Tanks should have a close-fitting lid that will not deteriorate or allow mould or bacteria to grow on it and drip into the stored water and any vents or openings should be covered with a fine mesh.
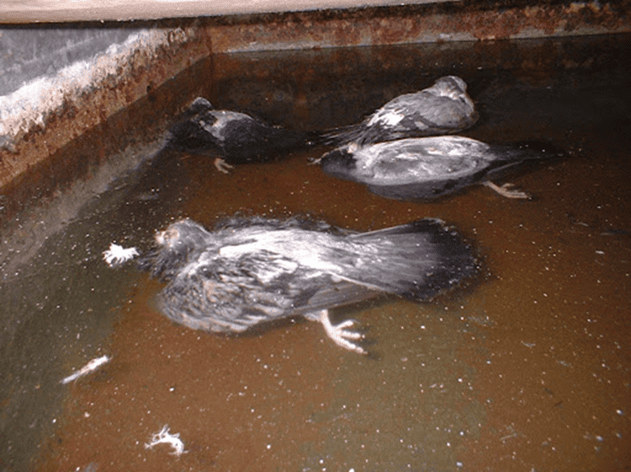
Figure 3: Contaminated water tank
Cold-water storage tanks and hot water vents
A modern indirect cold-water system will have an overflow from the hot water storage tank as shown in the diagram below.
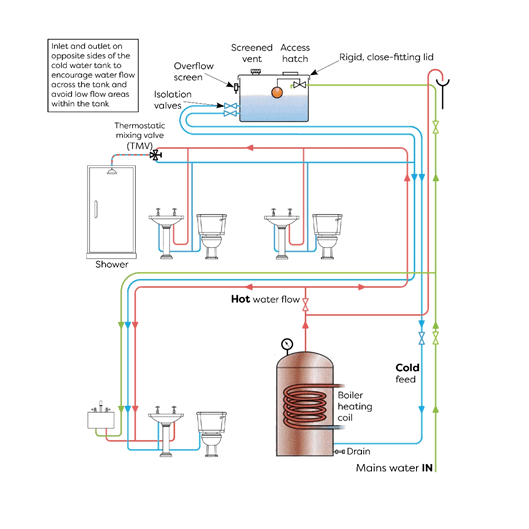
Figure 4: Modern indirect cold-water system with overflow from hot water storage tank
However, some older properties will have a system where the overflow from the hot water tank is to the cold-water storage tank in the loft (see below).
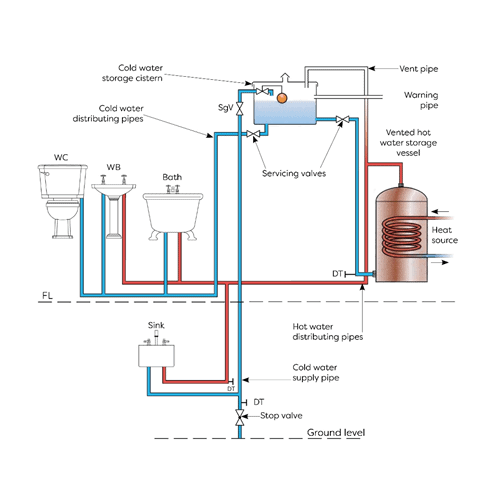
Figure 5: Indirect cold-water system with hot water overflow to the cold-water tank
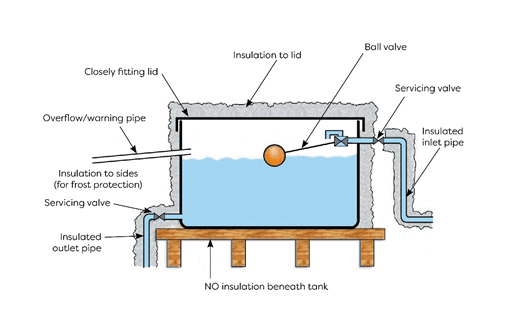
Figure 6: Cold-water storage tank
Indirect hot-water system
When using the hot water system, gravity provides pressure allowing water to travel from the cold-water tank via the outlet pipe and indirectly supply the hot water cylinder (see below).
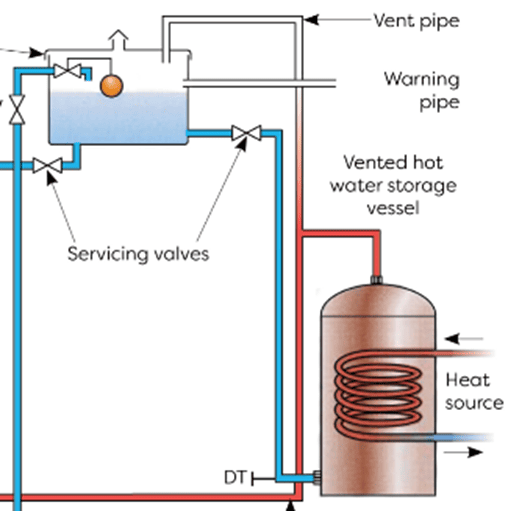
Figure 7: A closer view of the hot water cylinder connected to the cold-water tank, not specifically the vent pipe.
With a system like this, when the water temperature increases within the hot water cylinder, the water will begin to expand. Water at seventy degrees Celsius can expand to two or three per cent of its volume. Therefore, a good working cylinder must have the means for this expansion to take place and the vent pipe offers the solution. If a cylinder does not have a vent pipe or a means for the water to expand it will split and leak.
Under usual circumstances, the hot water will expand up the vent pipe to a level then drop back down to the hot water cylinder. However, if there is a malfunction, the hot water will continue to travel up the vent pipe and into the cold-water tank in the roof. At this point, you would hope to see water discharging from the warning pipe or staining to the ceiling from a leak and will be able to prevent a more serious problem. Unfortunately, if this is not spotted it can lead to disaster.
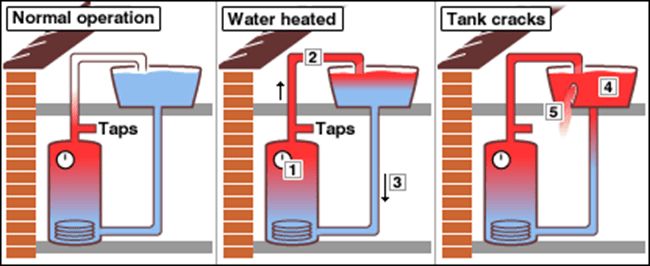
Figure 8: Failing hot water cylinder. The hot water continues up the vent pipe into the cold-water tank
Case study – Rhianna Hardie, 2006
In 2006, ten-month-old Rhianna Hardie was killed as a result of scalding water pouring into her cot. Rhianna lived in a house with a hot water tank that vented into the cold-water storage tank. The baby girl was showered with scalding water after the thermostat failed on the immersion heater in the hot water tank, causing the plastic cold-water tank to flood and burst.
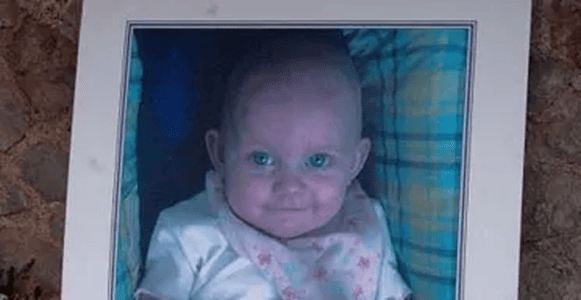
Figure 10: Rhianna Hardie
In this case, the thermostat malfunctioned allowing the hot water from the hot water cylinder to travel up to the cold-water tank in the loft. The immersion heating system in this case was a “fail-go” type, meaning that if the thermostat failed the water would continue heating, unlike modern models which cut out.
The water would have continued to heat and continued to rise through the vent pipe and although there must have been the tell-tale signs of water discharging from the overflow pipe, as this incident happened during the night this warning could not have been spotted. Instead, the cold-water tank continued to fill with the increasingly hot/boiling water until it eventually gave way and poured through the nearest ceiling which happened to be the bedroom of little Rhianna. It is a miracle her sister who was in the same room was not injured.
You do not have to be a parent to feel the pain for this family and what the poor child had to experience during this horrific accident. She was rushed to hospital but sadly died of her injuries.
The coroner, Michael Rose, said the case was among the most tragic he had heard in his 40-year career. He urged anyone with a boiler with an outmoded thermostat to check their heating system and warned that (at the time in 2006) 3.5 million defective boilers of the kind that killed Rhianna were still in use.
Building Regulation response
Following this disaster (and sadly others that had occurred beforehand), Approved Document Part G – Sanitation, hot water safety and water efficiency was reviewed. Within the current version (2016) it states in section G3:
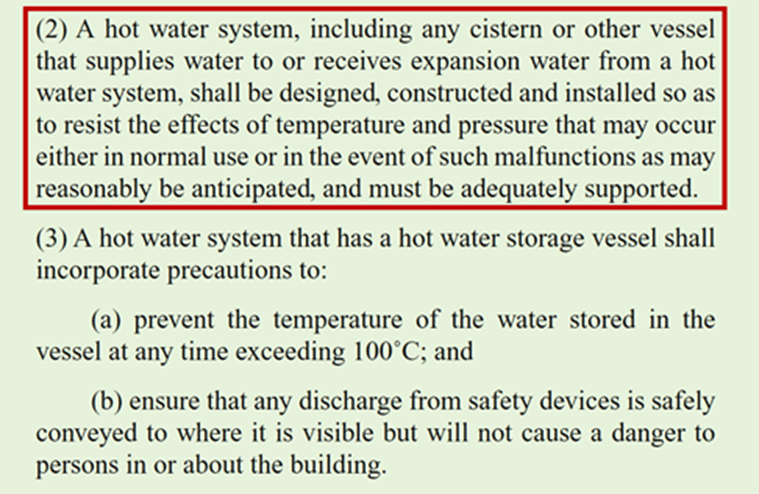
It then goes on to say:
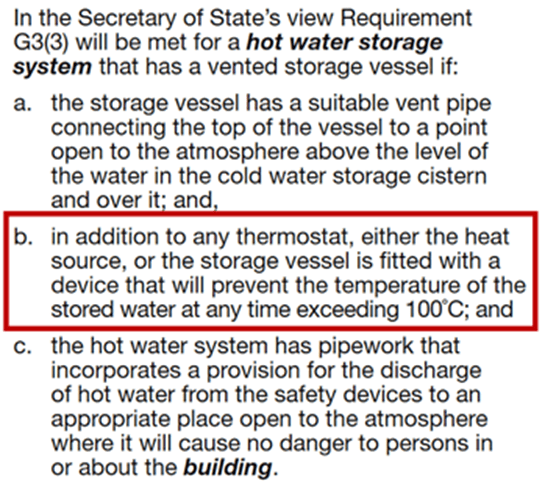
To minimize the danger from excessive pressure, unvented hot water storage systems should incorporate a minimum of two independent safety devices. These shall be in addition to any thermostat provided to control the desired temperature of the stored water. The selection of safety devices should take account of the physical location of the devices, and the design, configuration, location of components and performance characteristics of the system to which they are attached.
Though the above steps have been taken, it is worth noting that the position of the water tank is still not covered under current Building Regulations. Even though you might suggest that the tank be moved above the hallway, your recommendation cannot be enforced.
Though the above steps have been taken, it is worth noting that the position of the water tank is still not covered under current Building Regulations. Even though you might suggest that the tank be moved above the hallway, your recommendation cannot be enforced.
What can we do as surveyors?
The simple response to this must be to understand and recognise potential hazards to human health and to report on them, as appropriate. We must be able to identify the hazards and then determine the risk associated with the hazards. The HSE has a useful 5 step approach to this:
- Identify the hazard
- Decide who might be harmed and how
- Evaluate the risk (the likelihood or ‘chance’ of that harm occurring – risk will be high, medium, or low) and what precautions would be appropriate
- Record and implement the findings
- Review the assessment and update if necessary (clearly, not possible if you are visiting a property on behalf of a potential purchaser, but much more relevant for a residential property manager)
When evaluating the risk using a ‘Risk Matrix’ is helpful. An example is given below. (Source Larry Russen)
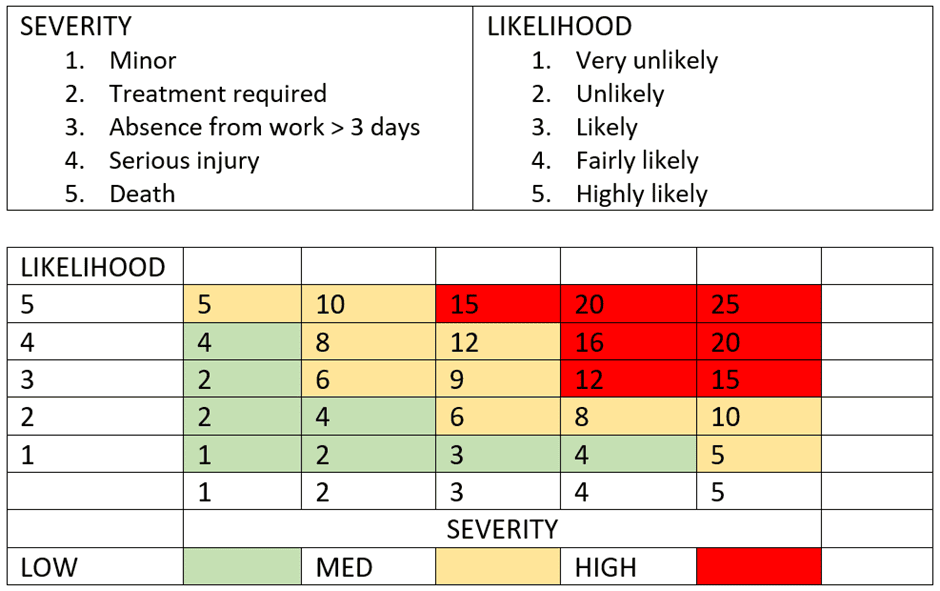
How such a hazard will be reported to the client will depend on whether the survey is level 2 or 3.
- Level 2 – the surveyor should identify the risk and explain the nature of the hazard
- Level 3 – the surveyor should also explain how to resolve or reduce the risks
But you also have a duty of care to the current occupier, even if they are not your client. Where a cold-water tank is positioned over a bedroom, I would rather be seen as over-cautious and suggest the tank be moved to above the hallway than find there had been a malfunction and boiling water had covered a bedroom where someone (possibly a child) was sleeping. A quick warning to the vendor could be the difference.
Fiona Kelly
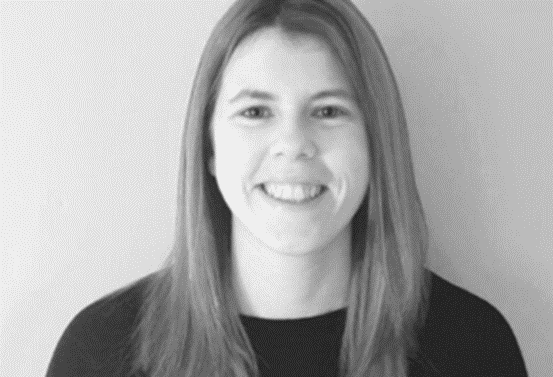
Fiona is Assistant Surveyor at Hannent Chartered Surveyors and a student undertaking the Sava Diploma in Residential Surveying and Valuation. Having made the career move last year from Events Management where Fiona managed large scale pharmaceutical meetings, she is now establishing herself within her new role and has a particular interest in planning and development.