Pitched Fibre Drains (Part 1).
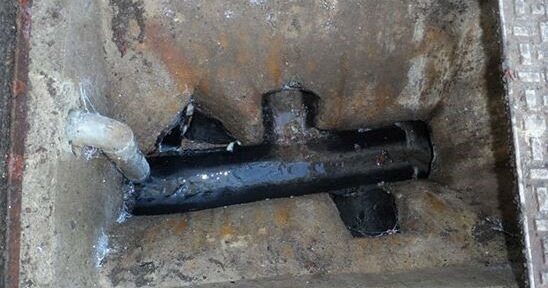
Inspecting Underground Drainage Systems
1.0 Introduction
To constitute a dwelling, a property must have independent cooking and washing facilities containing sanitary ware connected to a water supply and drainage system. Waste water is disposed of via internal above ground pipework to an underground drainage system, which is commonly connected to public sewers or can discharge to independent, private drainage systems (septic tanks and soakaways, cesspits or packaged treatment plants). Understandably, drains matter to people and every year SAVA receives several queries from home owners relating to drains both inside and outside the property – “ what should the surveyor have seen and what should they have reported?” In this article we will review good practice relating to underground drainage and look specifically at the issues with pitch fibre pipes.
2.0 Drainage systems connected to public sewers
The growth of piped water supply system to individual dwellings after the Public Health Act of 1875 also prompted construction of centralised below ground drainage system (famously in London the sewer system was designed by the engineer Joseph Bazalgette and was instrumental in relieving the city from cholera epidemics). Any design for underground drainage must fulfil multiple purposes, be self-cleaning, require minimal maintenance from the occupiers and provide sufficient removal of waste water designed to meet and exceed the occupant’s requirements. Historically properties built prior to 1950 are likely to have drainage systems based on the original designs of the 19th Century. The most common material was salt glazed clay drain pipes with socket and spigot ridged joints, as this was the most cost effective and available building material. Salt-glazed clay pipes remained the most common type until the 1950s when vitrified clay drain pipes with flexible joints were introduced. Other materials were also used including concrete, asbestos cement or plastic pipes. In a short period between 1950 and 1970, pitch fibre pipes were also installed. This sort of pipe has posed specific problems over and above other designs, so we are focussing on the issues surveyors need to address.
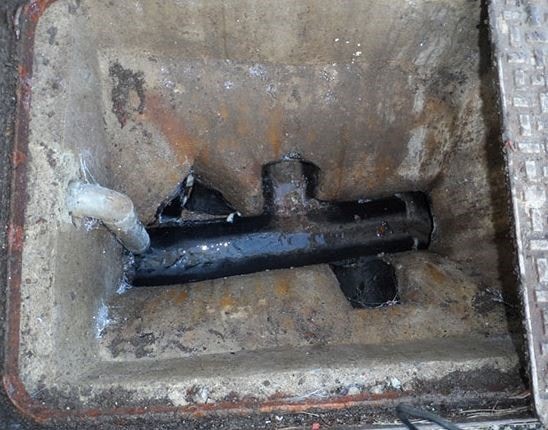
3.0 The problems posed by pitched fibre drains
Pitch fibre drains were made from wood fibre impregnated with coal tar, and while they have been shown to perform sufficiently when dealing with normal waste water, research has shown that they can react badly when subjected to large quantities of hot water, oils and fats. These can soften the tar and cause deformation and leaks. The design life of pitch fibre pipes is estimated to be about 40 years. This means that many will have reached the end of their life expectancy. In the worst cases, they can collapse, blocking the drain run. According to a “Review of Existing Private Sewers and Drains in England and Wales” published in 2003 by the Government Department for Environment, Food and Rural Affairs, it is estimated that there are around 50,000 properties with this type of drain. Some types of pitch fibre pipes were also reinforced with asbestos fibres and this can increase the cost of replacement. The pipes [made from pitch fibre] were relatively inexpensive and easy to handle and install. However, it became apparent that these pipes were susceptible to the delamination of their inner surface, ruining the integrity of the pipes. It was also discovered that, under normal conditions, they were susceptible to collapse under applied loading sooner than pipes made of more rigid materials.
4.0 Problems with identification
In cases where the sections of underground drains visible via inspection chambers contain vitrified clay drains, it is very difficult to identify whether there are out of sight sections of the drain run which are pitch fibre. One of the main problems with pitch fibre pipes is they are difficult to spot. This is because most change to vitrified clay channels as they pass through inspection chambers – easy to miss during a brief visual inspection. One recommended approach is to lift the chamber lid and set it aside. Then get as low down as possible so you can look up the drain run as far as you possibly can. Often the texture and colour of the pipe will clearly change as it meets the clay channels. In some cases, you may be able to see remnants of the black tar used to seal the junction. If the chamber is not too deep, you may be able to use a mirror and torch to look up the drain. You could even take a photo along the drain if you have a ‘selfie stick’ although be ready to move if you hear a gurgling sound!
We are not suggesting you adopt this approach with every property but when you are inspecting a dwelling built between 1950 – 1970 you should follow this trail. If pitch fibre drains are identified or suspected a recommendation for further CCTV investigation of the drains can be justified on the grounds of their known estimated life expectancy, the possible issue with insurers and the need for further investigation. The likelihood of failure can be justified and repairs can be of significant cost and particularly complicated where drains are shared or run over adjacent properties.
PROBLEMS WITH INSURANCE
According to the Financial Ombudsman Services, most insurance policies will cover damage to underground drains that serve the insured property so long as those pipes are the responsibility of the policy holder and the damage is accidental. However, such policies may contain several exclusions, notably wear and tear, gradual deterioration and faulty workmanship or design. They report that some insurers may specifically refuse to pay claims relating to pitch fibre pipes even though the policies do not specifically exclude them due to the above. There is comprehensive consumer guidance on their website on how policy holders should approach any potential claim but this will not be straightforward. However, some more modern policies are much more open and specifically exclude coverage of pitch fibre drains. Consequently correct identification may have considerable financial implications for the home owner.
5.0 Limitations to inspection
It is worth pointing out that on many properties there are no drain inspection chambers within the vicinity of the property or if they are present, they can’t be lifted. (This can be due to them being in an inaccessible location, being too heavy to lift during the course of a normal inspection or there being a risk of damage if they are lifted). In such situations a limitation of the inspection should always be recorded in the site notes, ideally with a photograph. In such a situation a constructive comment in the actual report about the presence or lack of inspection chambers and their suitability for inspection can be helpful for your client and help to manage their expectations.
6.0 Reporting on Drains in the HCS
When applying the condition rating (assuming you have carried out a Home Condition Survey) a brief explanation of potential risk factors such as root damage from very close trees or hedges, instability of extensions, conservatory foundations affecting the drain run underneath, visible signs of ground movement through the assumed drain lines, etc. will contribute to your justification for the Condition Rating you attribute to the drains. The protocol can be helpful here, and as with other elements in the property, if you feel it is inappropriate to attribute a CR3 to all the drains where you feel only one part may be suspect, you can report on more than one drain – splitting the element up. The approach for RICS survey products is different and we will return to this in another article. In circumstances when there are no inspection chambers, or the chamber lids could not be lifted and there are no known issues (visible or that you can deduce from local knowledge, experience etc) that could have a negative impact on the performance of the drains, awarding a Condition Rating 1 may be appropriate but with a clear description of the limited scope of the inspection and supported with photo evidence of the limitations and surrounding area of the assumed drain run. But think carefully about risks to the drains that may have occurred since they were laid and consider the expectations of your client. In most causes where no access is possible, a Condition Rating 1 is very unlikely to be correct and could lead to an unhappy client and a possible complaint. Your client – and their solicitor (should it all get litigious) – will rightly and literally comprehend the reported condition as “No repair is currently needed. Normal maintenance must be carried out.” Later, if an issue manifests itself the surveyor’s liability will be challenged with minimal chance to defend. In such instances, rating ‘Not Inspected’ is most likely to be appropriate but you should justify why it was not inspected and provide an adequate and comprehensive reason for the limitations. But this must be judged on a case by case basis. If there is any doubt in your mind as to the efficacy of the drains even when clear access to an inspection chamber is possible, it would be sensible to allocate a Condition Rating 3, suggesting further investigation due to risks relating to the drains and referring to the fact that on the date of inspection you were not able to inspect the drains. Pitch fibre drains will fall into this category.
The following wording with appropriate amendments might be adopted in similar situations:
“The property has mains drainage connected to a public sewer system, however no inspection chambers could be located within the boundaries. Access to the drains is …. [either state position of inspection chambers if identified or describe restriction limiting access to drains.]”
Then, if no visual issues identified:
“Whilst no deficiencies were observed via visual inspection, the location of the drainage access should be confirmed by your conveyancer for future reference.”
If some visual defect indicators are present (e.g. bad smells, signs of flowing sewerage and/or property located in high risk areas of surface water flooding, etc.) then CR 3 recommending further investigation is the right option. If you are able to lift the drains cover then photographs should be taken and stored with the site notes and uploaded within the HCS report clearly describing condition of the benching, drain pipes, any objects present within the drains (roots, debris, sediments, etc.). If possible, a flow of the drains should be observed but you should ensure that it is safe to do so (be very aware of the occupants of the property at the date of inspection). A similar approach can be adopted with private drainage systems with addition of a comment about type and frequency of disposal. Finally, all drainage systems (drain runs, inspection chambers, septic tanks, cesspits, etc.) present within boundaries of the subject property must be included in the BCIS calculation. The reinstatement cost for underground drainage can be very substantial and it is often left out or underestimated. Such works can make up a large proportion of the reinstatement value therefore it is crucial that surveyor estimates are as accurate as possible, so the property is not underinsured.
Drains and the value of local knowledge.
HILARY GRAYSON reports:
“When I was a practising surveyor at one stage I worked for the London Borough of Bromley, primarily packaging up development land for private sale. Being an outer London borough, this was usually for residential development. One site that we sold was in Biggin Hill. The land was immediately adjacent to Biggin Hill Airport. Housing in Biggin Hill varies in age but there was not a lot there dating before the second world war, when the airport was an RAF base. Most of the older properties date from around this period and were built to house the base workers. By the mid-1980s, when I was at Bromley Council, Biggin Hill had begun to gain a reputation for drainage problems. This caused us considerable headaches when we were selling the land and I remember commissioning endless drain surveys. The reason for the reputation was simple – the main sewers were apparently installed at the time the RAF base was developed. The priority then was not to create a long lasting public sewage system but rather to beat the Luftwaffe. Consequently, and particularly adjacent to the airport, the public sewers were not great and some of the connections to the private drains on people’s property were distinctly sub standard. ”
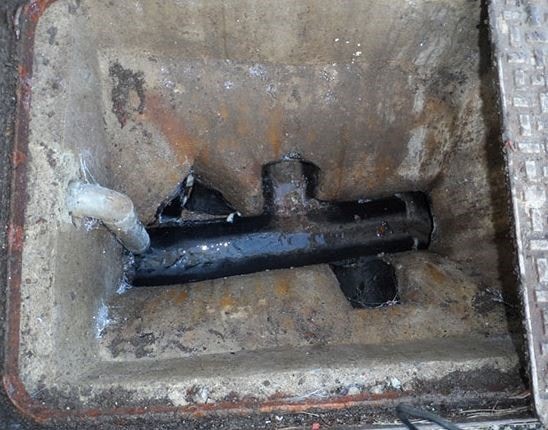