Gas Busters (Part 1).
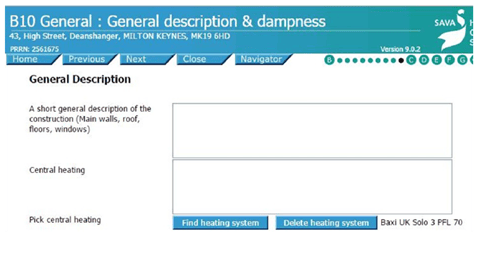
With most of the UK population owning a gas boiler, it’s probably worth paying that extra bit of attention to the quality and, more importantly, the safety of any installation. Accepting the fact that Surveyors are not registered gas engineers and can’t start breaking the boiler into bits to inspect it, there are some basic observations that could make for a better quality of assessment, and might even save someone’s life!
The rules
The gas safety regulations, like many legislative documents, are not an enjoyable bedtime read. However, there is one section which I have always considered to be the cornerstone of maintaining and ensuring the safety of any gas appliance. This is regulation 26(9) of the gas safety installation and use regulations 1998.
The regulation basically states that there are 4 fundamental considerations to ensure a safe gas appliance:
1. The effectiveness of any flue
2. The supply of combustion air
3. Operating pressure or heat input
4. Its operation as to ensure its safe functioning
Now there is a reason I really like this little piece of legislation and it’s primarily because, if we always consider these 4 items at every job, we are almost certain of never leaving an appliance in a condition where it could kill somebody, and that’s the really important bit in all honesty. You can have scruffy installations with pipes all over the place, inadequate clipping etc., but if it’s not dangerous, it’s not a problem.
So the slightly more difficult consideration is to establish a methodology of checking some of these requirements given limited knowledge and experience in this area.
The basics
The Product Requirements for the HCS are completely unambiguous when it comes to services:
“When applying Condition Ratings to any of the ‘services that kill’ if no recent test certificate is present in accordance with the guidance from the relevant competent persons scheme, then a Condition Rating 3 should be applied on the basis that further investigation is needed”.
Also, when it comes to the boiler itself, the HCS enables you to automatically provide your client with additional useful information about the boiler. It is essential that you include this information in the report. We recently had a potential complaint about a boiler which had failed almost as soon as the new owner had moved into the property. Luckily the complaint was easily dealt with as the surveyor had correctly used the Boiler Database to populate this bit of the report. The report clearly stated when the boiler had been manufactured – manufacture had ceased about 12 years previously – and although the exact date of installation was not known it was clear from the report that this was not a new boiler.
Use this section of the report as follows:
At data entry section B10 select ‘Find Heating System’:
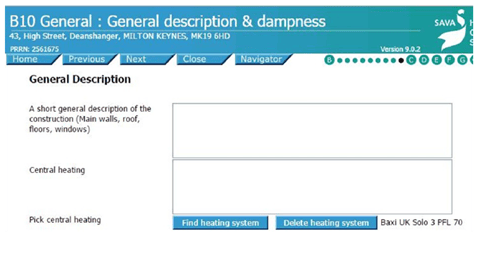
This directs you away from the HCS to the Boiler database. Enter the make of the boiler and click ‘search’:

You will then get a list of possible boilers. Go through the list to find the correct model. Select the correct model and the report will automatically populate with generic information about this boiler:
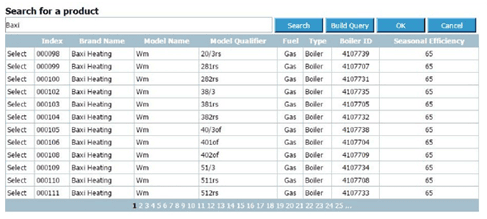
Even if a recent test certificate is present there are some additional checks that a surveyor can do to ensure that the system is in good condition and we will start by looking at visual checks that a surveyor can make of the flue.
Flues
The definition of a flue is a duct, pipe, or opening for conveying exhaust gases from a fireplace, furnace, water heater, boiler, etc. to the outdoors.
One by-product of burning gas in a boiler is the lethal gas carbon monoxide. The trouble with carbon monoxide is that it has no taste, colour or smell and people can die from carbon monoxide poisoning without being aware of the danger.
The effectiveness of the flue is predominantly governed by the fact that it’s the right flue for the appliance which can be checked against manufacturer’s instructions. Of course, when undertaking a survey you are unlikely to have access to the manufacturer’s instructions for the boiler. Consequently, as a surveyor, all you can do is to check for generic issues that might give cause for concern.
The age of the appliance will determine whether you need to look for signs of corrosion. Older metallic flues tend to have a pressed seam along the length, which particularly if they have been installed facing downwards, are susceptible to heavy corrosion. So this is worth a quick check if achievable (if you have a little mirror on the end of an extendable pole, these can be very useful for checking these areas.) Corrosion within a flue structure can cause a mixture of fresh air and the products of combustion (vitiation) and this can create real danger for a gas appliance.
Another type of flue which can cause particular problems is a flue for an appliance which is not located on an external wall. As a consequence the flue has to run some distance to the outside. Sometimes this might be in a roof space or routed through a ceiling or wall void. It may be boxed in and pass through a room and it might pass through another dwelling. Such flues are normally associated with flats or apartments, where they might be routed between properties, but they can be found in houses.
Concealed flues of this type came about with the introduction of fan-flued gas appliances in the mid 1990s. This allowed boilers to be installed away from external walls. Clearly this provided builders and architects with greater flexibility and they could design new-build and refurbishment properties with boilers installed on internal walls.
This practice became progressively more popular from 2000 onwards and, according to the Health and Safety Executive (HSE), the vast majority of affected systems are thought to be located in new build flats and apartments completed since 2000. It is, however, possible that other types of home may have similar central heating systems installed, particularly conversions.
The problem with such flues is the fact that ‘out of sight is out of mind’ and that they can fall into disrepair without anyone realising a problem exists. The risk, particularly of carbon monoxide poisoning, is such that the HSE particularly references ‘flues in voids’.
According to the HSE:
“Gas engineers are legally required to check the flue after carrying out any work on the boiler. This will include a visual inspection. Similarly, when an engineer installs a boiler they need to ensure that it can be used without constituting a danger to anyone; this would include checking whether the flue is safe. The original installer and every subsequent servicing or maintenance engineer need to be able to check that:
*the flue is continuous throughout its length;
*all joints are correctly assembled and are appropriately sealed; and
*the flue is adequately supported throughout its length.
Unless the gas engineer can make these checks they cannot ensure that the flue from the boiler is safe in order to comply with their legal duties. This necessitates the provision of appropriate inspection hatches in the ceiling (and, where relevant, stud wall).”
Originally, the technical guidance provided by the gas industry for systems without inspection hatches was that they “were not to current standards”.
However, in 2011 revised technical guidance was introduced which requires inspection hatches to be fitted in properties where the flue is concealed within voids and cannot be inspected. The homeowner (or landlord etc.) had until 31st December 2012 to arrange for inspection hatches to be installed.
Any gas engineer working on such a system after 1st January 2013 has to tell the homeowner that the system is “at risk” in accordance with the Gas Industry Unsafe Situations Procedure (GIUSP) and, with the owner’s permission, will turn off the gas supply to the boiler so it cannot be used.
As a rented property should have an annual Gas Safety Certificate, the chances are that a property with an internal boiler that has been previously rented will have a compliant flue – so inspection hatches will have been created. Without them a Gas Safety Certificate could not have been issued.
Reporting
However, a home owner of a property that has not been rented may be oblivious to the risks.So, how should a surveyor react if they survey a property that has a concealed/hidden flue without inspection hatches?
The Gas Appliances are reported in detail at F2. The suggested wording when reporting on a gas boiler for the HCS in all situations:
All gas appliances, including your gas boiler, gas cooker and gas fire should be safety checked once a year and serviced regularly according to manufacturer’s instructions by a competent person. The Gas Safe Register is the official gas registration body for the UK. By law all gas engineers must be on the Gas Safe Register. If gas appliances are not regularly serviced and safety checked the occupants could be at risk and in possible danger of carbon monoxide poisoning.
If there is no evidence of a Gas Safety Certificate then the following can be added to justify CR3:
There was no evidence of a recent safety check or service.
Remember, if there is no Gas Safety or service record, it is important to also report this at Section C, in this case selecting ‘boiler’ from the drop down menu.
If you inspect a property with a concealed flue then it should still be CR3, but we suggest you report it as follows:
All gas appliances, including your gas boiler, gas cooker and gas fire should be safety checked once a year and serviced regularly according to manufacturer’s instructions by a competent person. The Gas Safe Register is the official gas registration body for the UK. By law all gas engineers must be on the Gas Safe Register. If gas appliances are not regularly serviced and safety checked the occupants could be at risk and in possible danger of carbon monoxide poisoning.
In this case the boiler has a concealed flue with no inspection hatches. This means that the system is “at risk” in accordance with the Gas Industry Unsafe Situations Procedure (GIUSP).
Under C6, Recent Testing, there is no facility to mention concealed flues. So, in such a situation, you should enter the matter of the concealed flue at C7 using the wording above and verbally report your suspicion to the agent or property owner.
The important factor to always consider when dealing with any property which has gas appliances installed is to err on the side of caution. Unless you happen to hold full gas safe approval for domestic gas work activity, there is a limit to what you are able to do in order to accurately establish the safety of an installation, and as such, it is wise to never report on anything which you feel falls outside your scope of knowledge. It is all about demonstrating that you have taken reasonable steps to visually inspect any gas installation and identified any concerns you may have, without ever formally suggesting that you have deemed the installation to be completely safe because, unless you are able to break into an appliance and check gas rates, burner pressures, flueways and ventilation, you will be unable to make that judgement.